So I debating of trying a new mold where I have the vertical ribs of MDF with no camber (planed perfectly flat) glued together and then profiling a sheet of 3/4" MDF to lay flat on top. The sheet would be cnc'd from 3/4" in the center down to about 1/2" at each end to give me roughly 5mm of camber.
I'm thinking of profiling a few sheets with varying camber heights. This way I can leave the heavy bottom flat mold in the press and swap out a light profiled sheet.
Question is, do you think MDF is the appropriate choice of materials for the flat camber sheet? It would be nice to use aluminum, but the cost of a 3/4" sheet is hard to justify.
There would be the usual 3 sheets of aluminum on top of the MDF (2 top and bottom of my blanket and one for the layup).
Maybe use particle board instead and seal the profiled surface with something to harden it....
Debate..................
Camber Mold...
Moderators: Head Monkey, kelvin, bigKam, skidesmond, chrismp
-
- Posts: 73
- Joined: Mon Feb 07, 2011 8:39 pm
I typically do an early rise tip/tail with camber between the bindings. Here are a few pics of my setup.
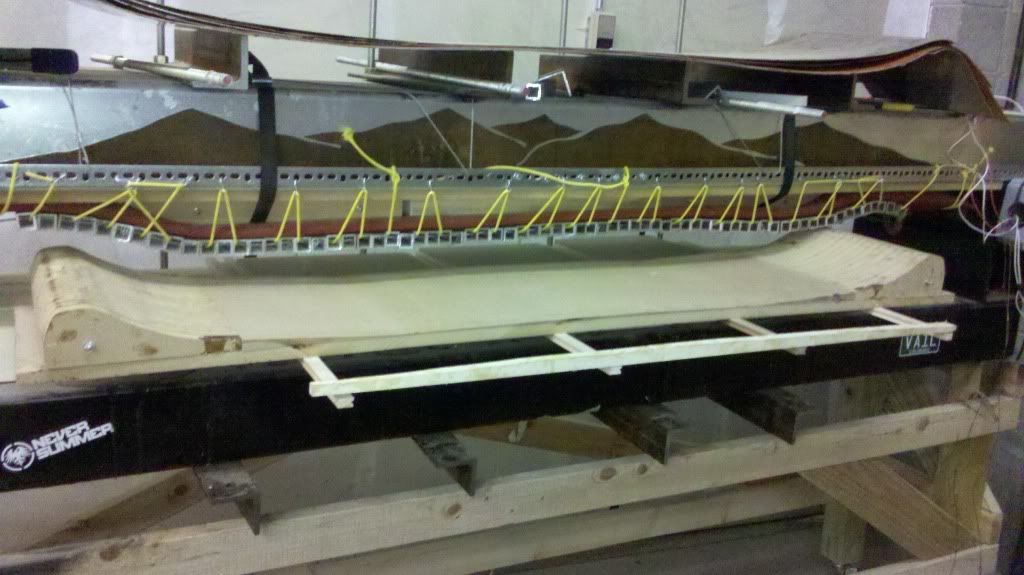
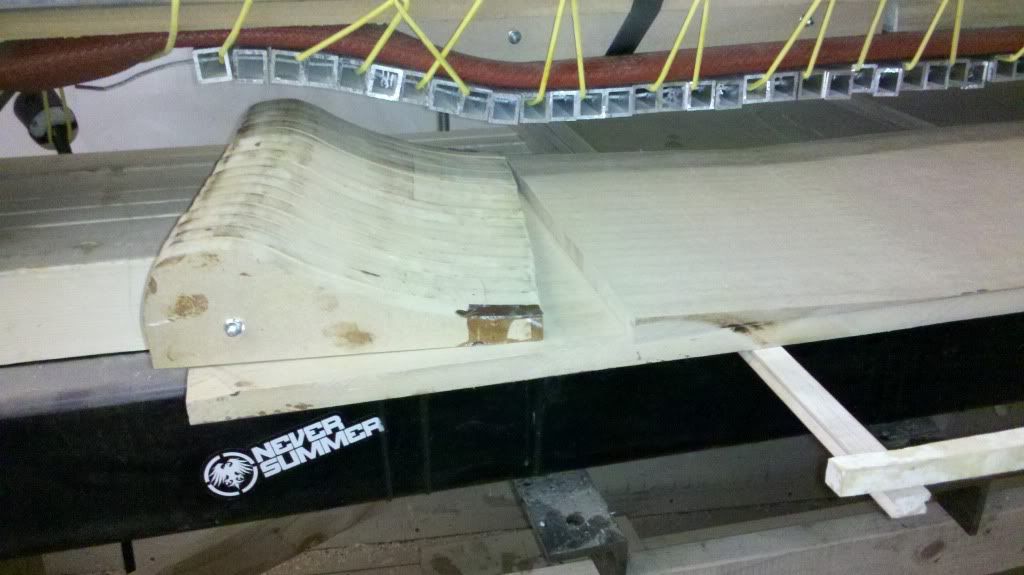
The tip/tail spacers are removable. They sit on a 3/4" MDF base. The mold is glued to the base so it is one unit I can move in and out and just replace the tip/tail molds. The key to this set up is making sure your CNC is extremely accurate with the end height dimensions although the aluminum does help if I have a small difference in height. I could easily make a full camber plate if I wanted. The ends of my mold would be "0" height.
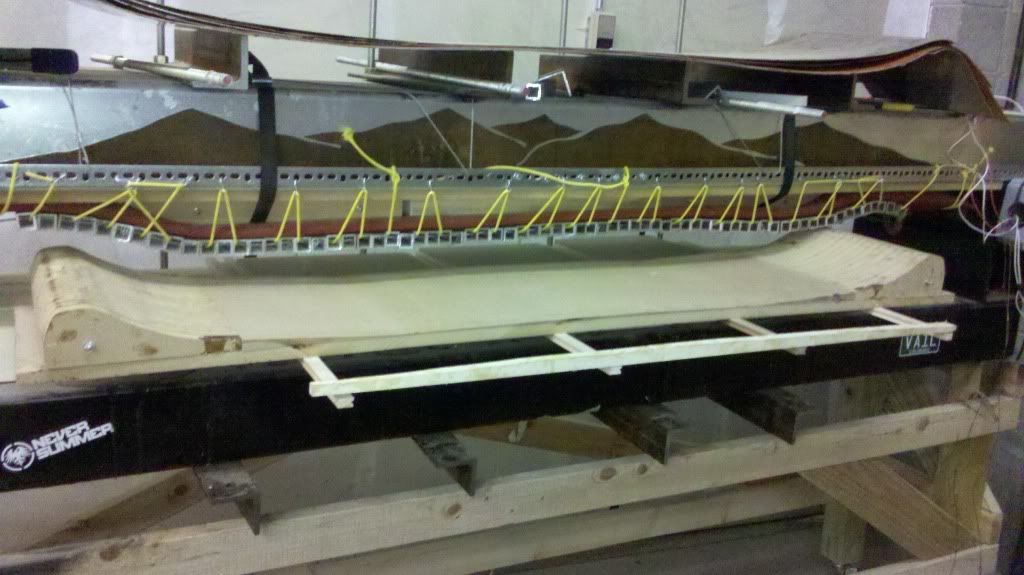
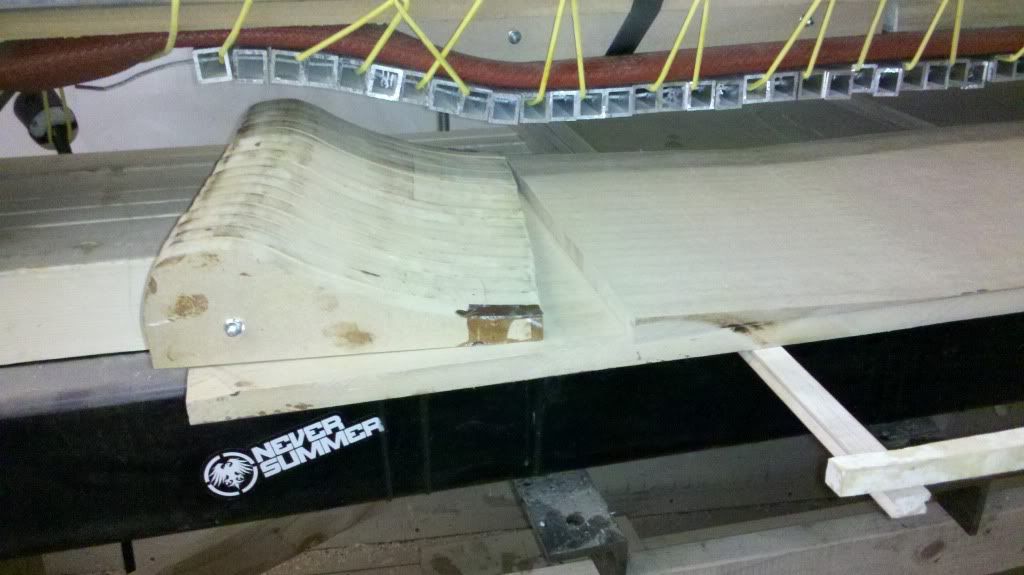
The tip/tail spacers are removable. They sit on a 3/4" MDF base. The mold is glued to the base so it is one unit I can move in and out and just replace the tip/tail molds. The key to this set up is making sure your CNC is extremely accurate with the end height dimensions although the aluminum does help if I have a small difference in height. I could easily make a full camber plate if I wanted. The ends of my mold would be "0" height.