This is used to cut the base:
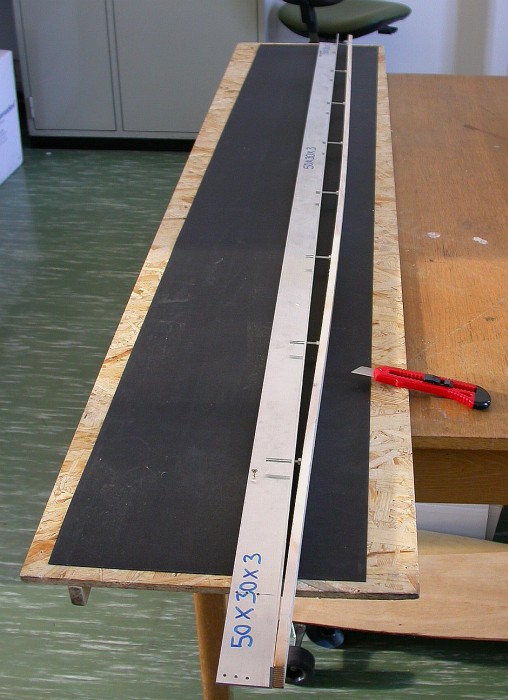
Then I glue the orizontally laminated core (3ply birch plywood)
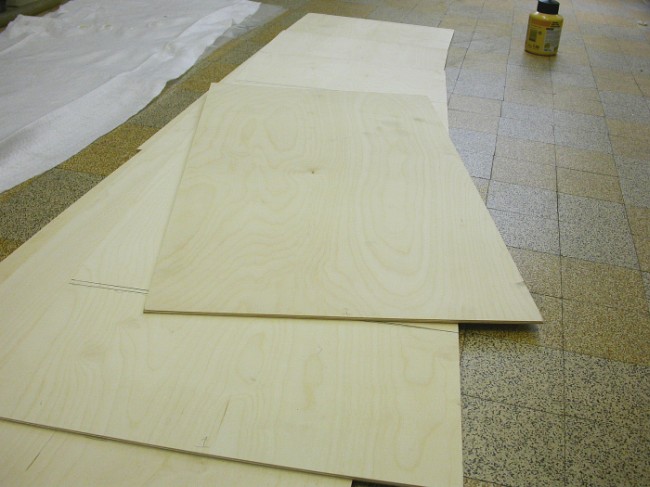
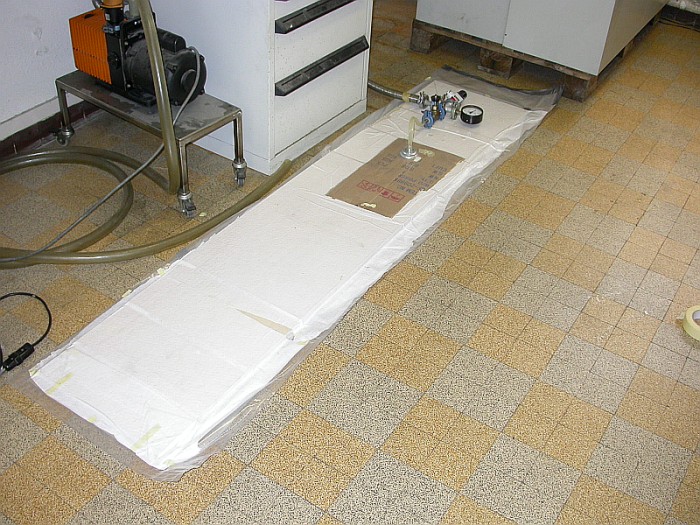
Then I machine the core: it is 4mm think at the tip and tail and 12mm thick in the centre.
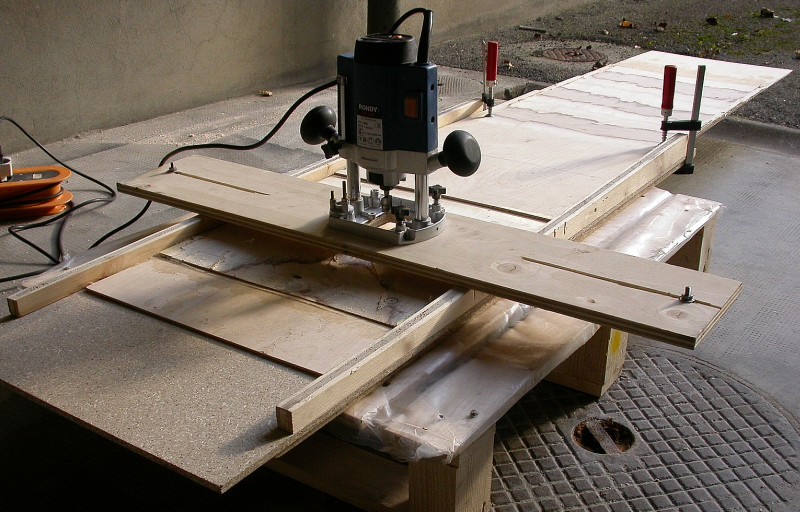
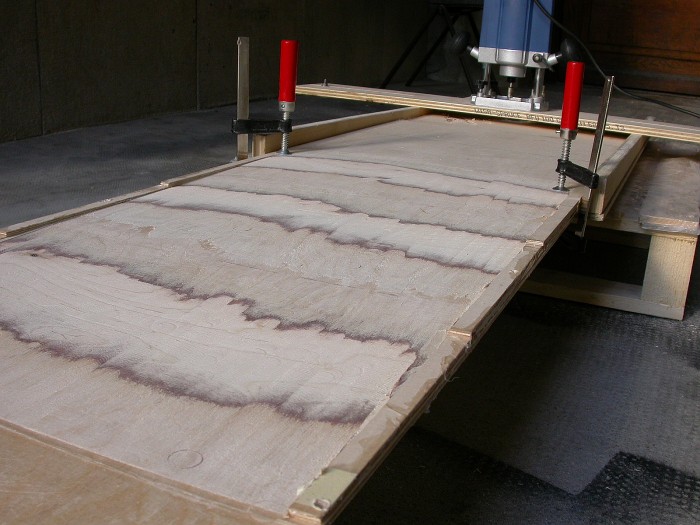
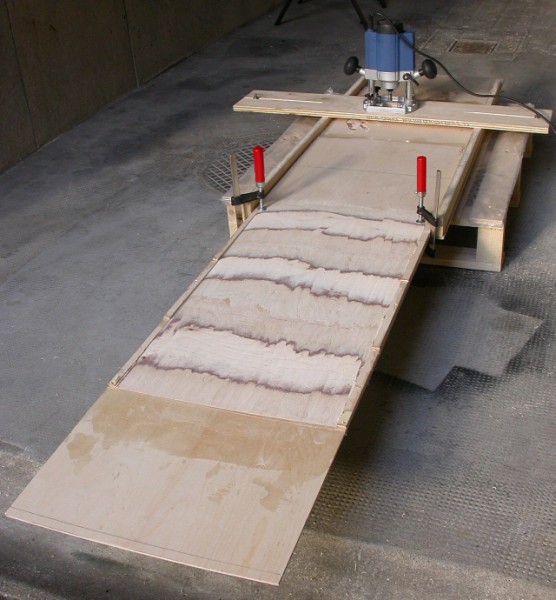
I bend the wood with hot water
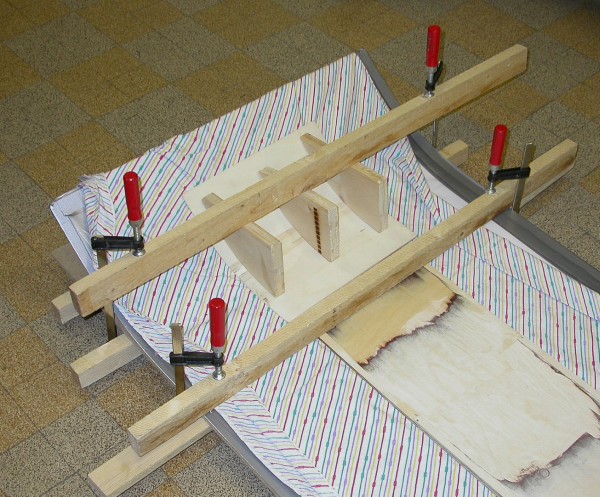
I usually do not put the edges in the tip and tail

then lamination and pressing under vacuum (glass: 300g/m2 biaxial and 425g/m2 UD between the base and the core and 425g/m2 UD as top layer )
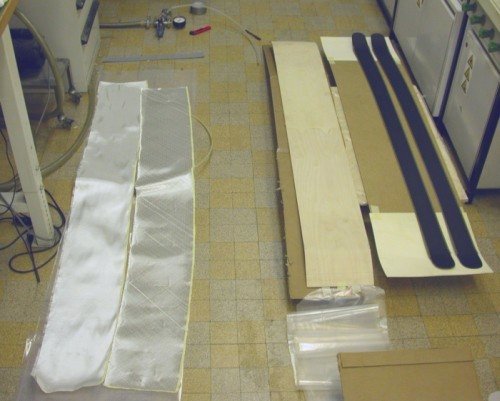
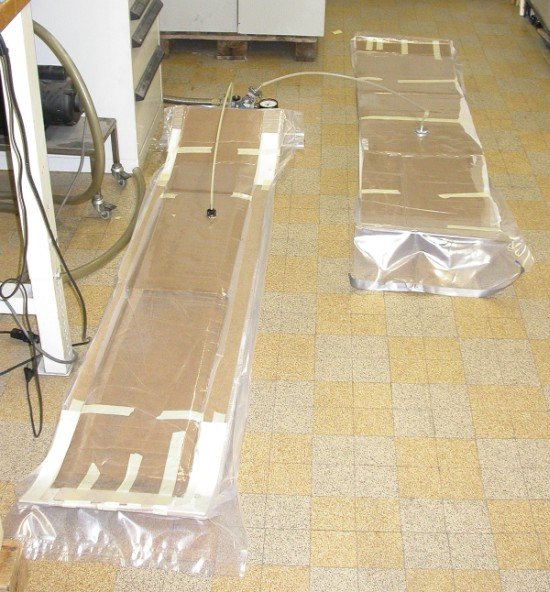
They I cut out the skis form the board with a "kataba meiko"
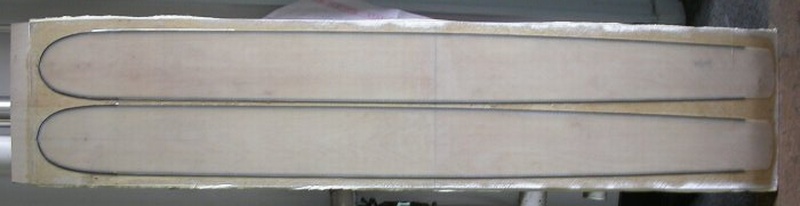
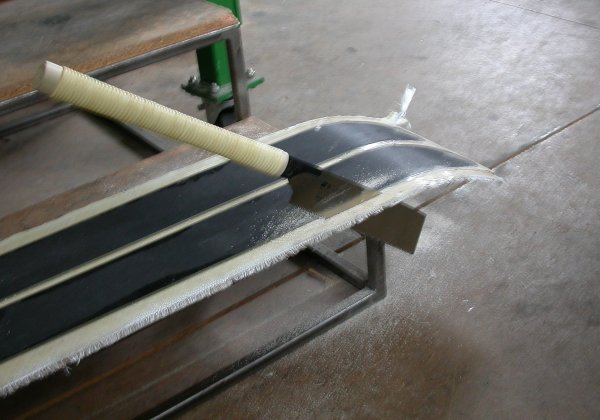
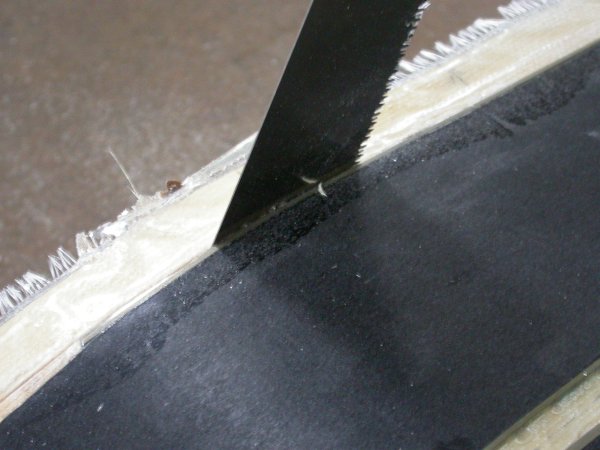
Here they are


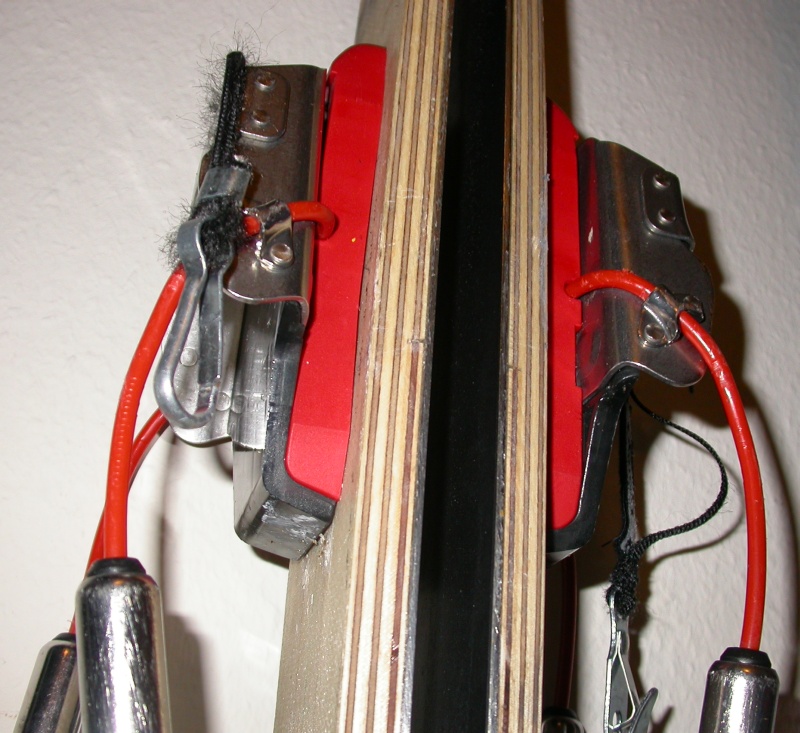
I called them the "()", that is double parentesis. They are somehow like the Kananas: inner radius is about 25m, on the outer edge they have a very small reverse sidecut; they are about 90mm wide. Actually I wanted to make something different, but I made a mistake in cutting the base, so I recycled the base for these ones.
I tested them in Les Paccots (CH). This is a tiny resorts in the "pre-alpes fribourgeoises".
http://www.les-paccots.ch/haut_int.php3 ... =0|0|2|3|5|
I love this kind of places. I had also my TUA OneTen, that I used in the morning. When I do testing I always have a backup pair, just in case… Then in the afternoon I picked up the "()".
They are nice when I ski them parallel in piste; in tele turns, I found difficult to keep the inner ski on the edge. I have Crispi CXA, and I have already noticed that it requires some effort to put a 90mm ski on the edges; I can do that, but it is not fun. Probably 80mm is the limit for these boots.
In off-piset (powder) they were nice of course. But 100mm or even 120mm at the centre are even better.
I think that if I must choose only two pair of skis, I would pick up a 110-75-100 for piste and backcountry (in variable conditions) and a 100mm or even 120mm wide ski (standard or reverse sidecut) for the pow-days. 90mm wide skis are not more forgiving in piste than a 110mm (at least for me) and they are not so impressive in the powder as the really large ones.