The trick is to use ultralight MDF, found at most specialty lumber suppliers. I used 3/4", but it is available in other thicknesses. It is porous and you can pull a vacuum through it. The top skins are not porous and needs to be cut away. The sides are sealed with duct tape.
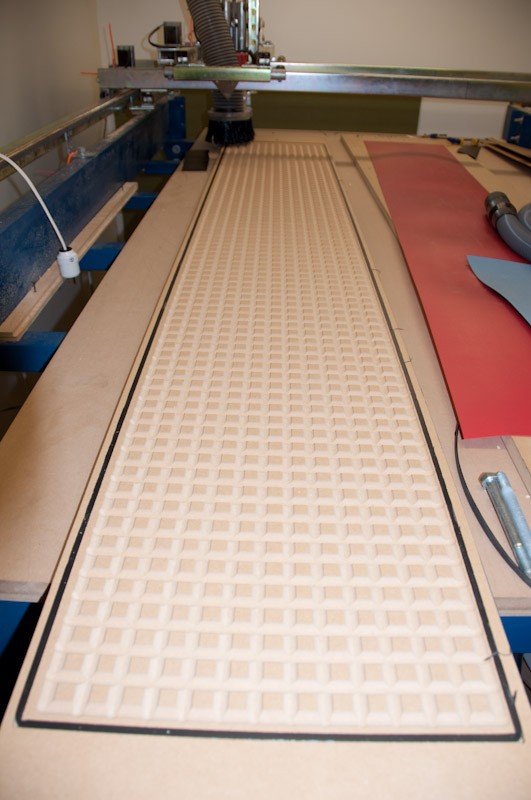
I cut a plenum pattern into the bottom of the baffle board and put gasket tape around to seal.
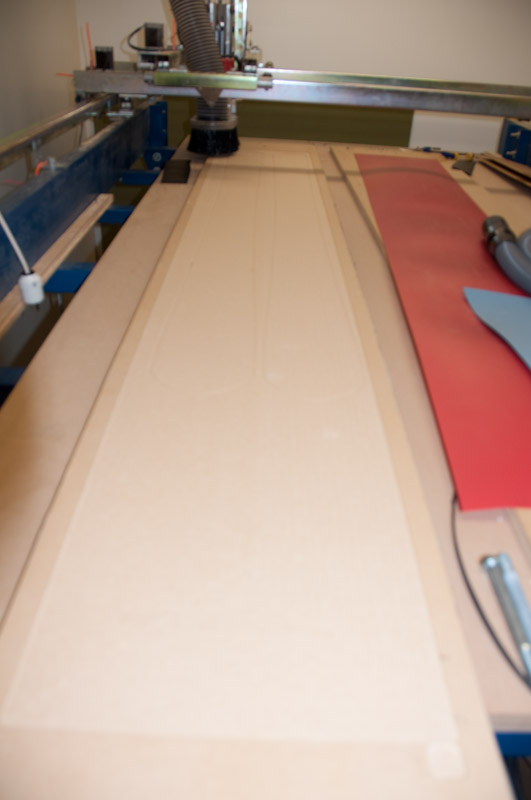
The top is surfaced.
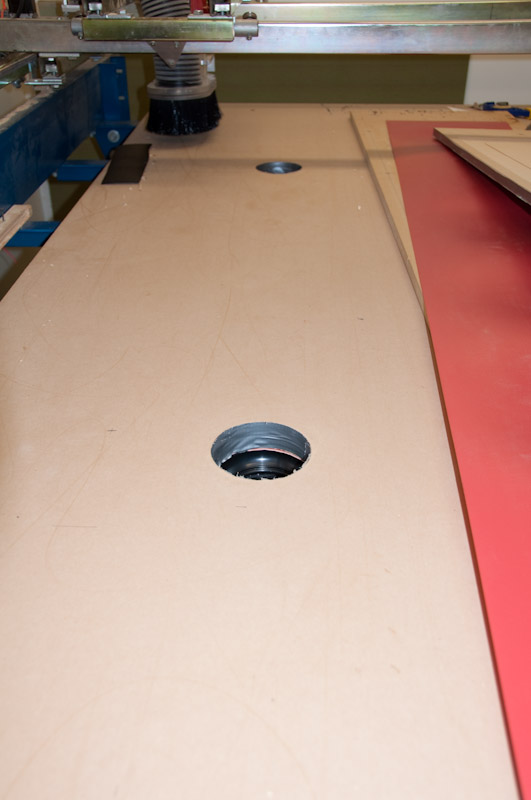
Holes are cut in the top of the table.
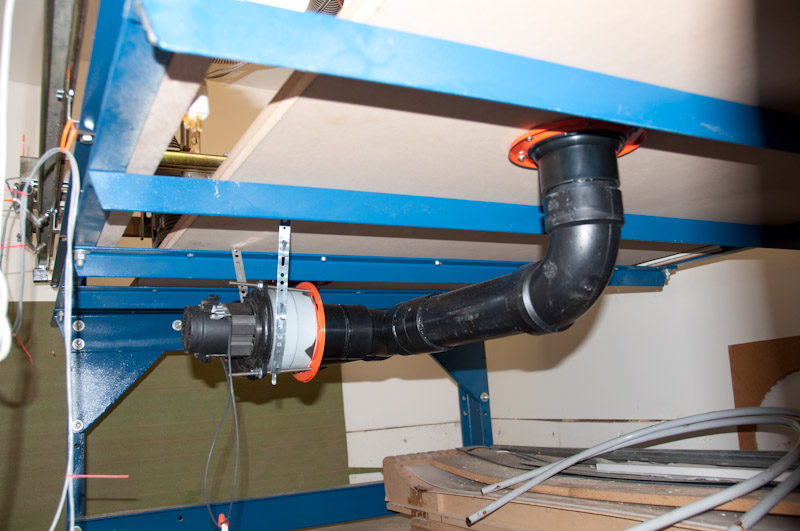
Underneath. ABS plumbing parts and a vacuum motor. Rated to 104cfm, but a strong shopvac would probably work.
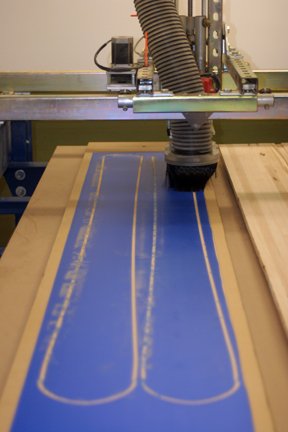
In use.
Once the vacuum is turned on, the base material or core is held very tightly. I can't move it unless I break the vacuum. I think you can adapt it for hand routering by making a small table/ stand with a couple of holes and grooves cut for the vacuum. The baffle board would be cut from the ultralight mdf and would be the hold down and also the template.