
I pressed the flange back and welded it into position
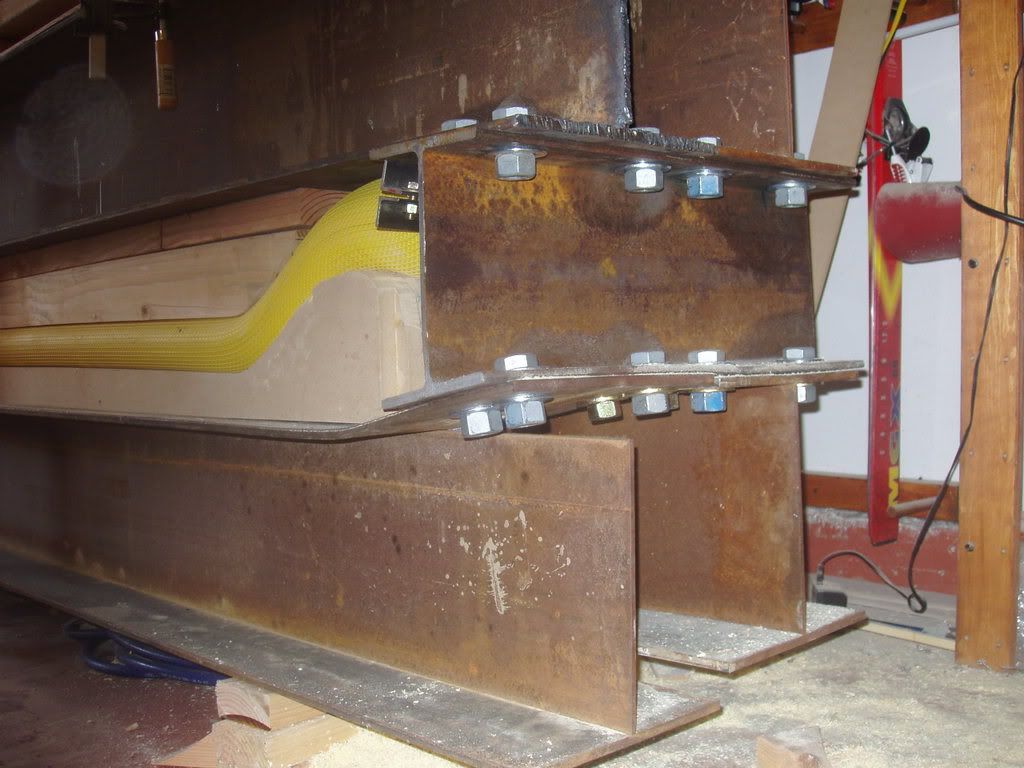
The discussion was pretaining to the way the beams were held together. Bolted on the inside flange and how this does not maximize the srength of the flange. I took this into consideration and after making calculations and discussing design options, I started on the rebuild.
Here is the press with the bottom beams in place.
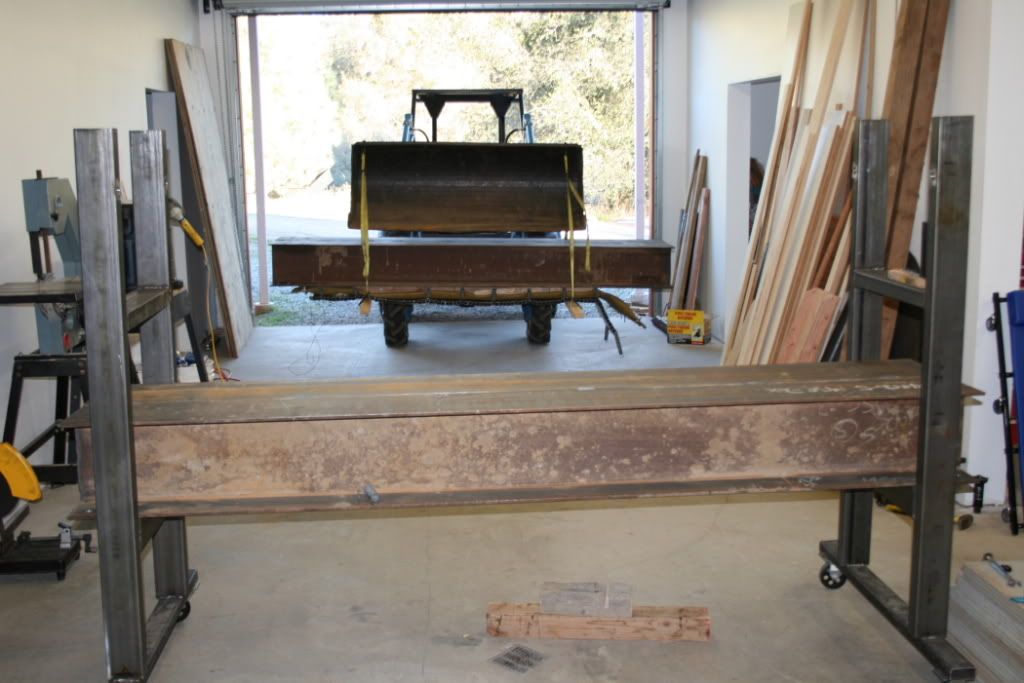
Lifting the upper beams into place.
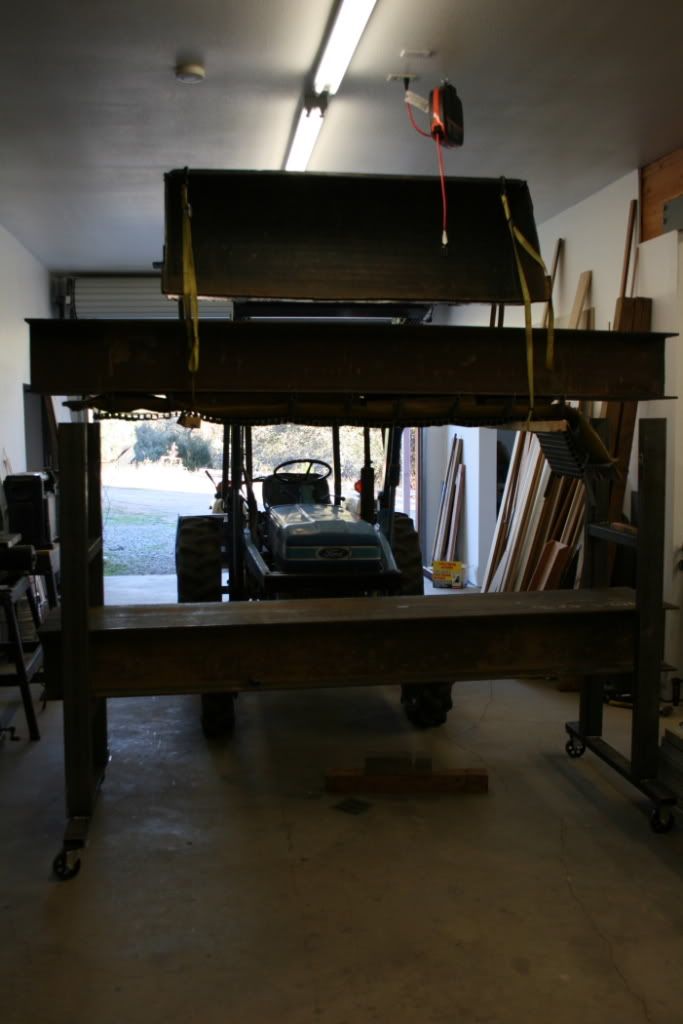
I wanted a height adjustable press to make loading the lay-up easier. So I used some pins to lock the upper beams into place. Had problems finding tube and pins that mated up good. The pins needed to be in the area of 1" solid.
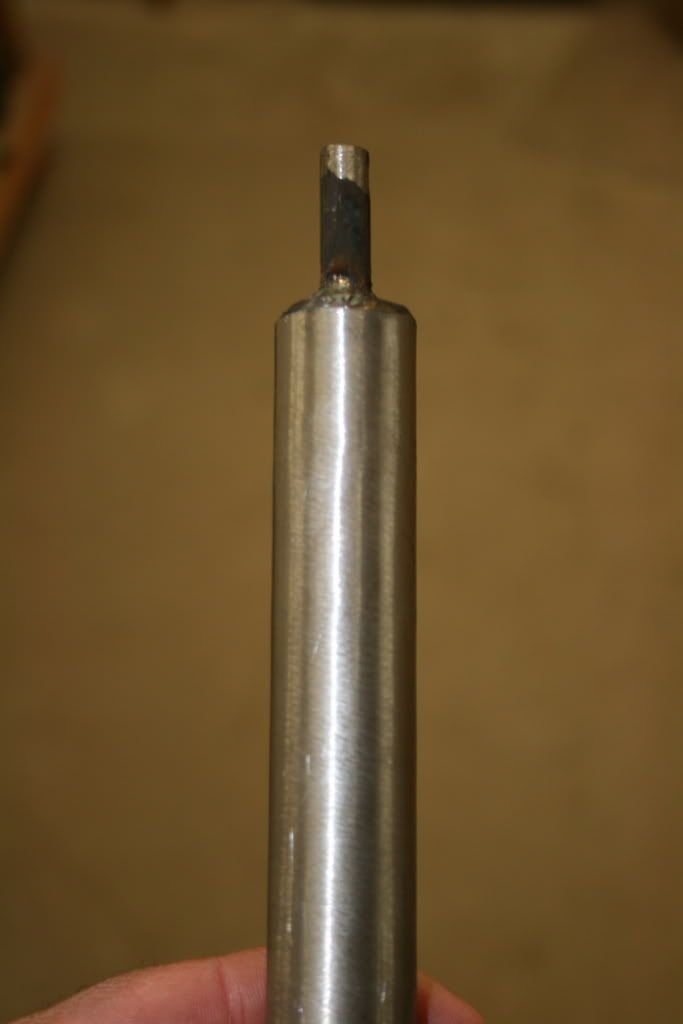
Here is the pin in the sleve locating the upper beam.
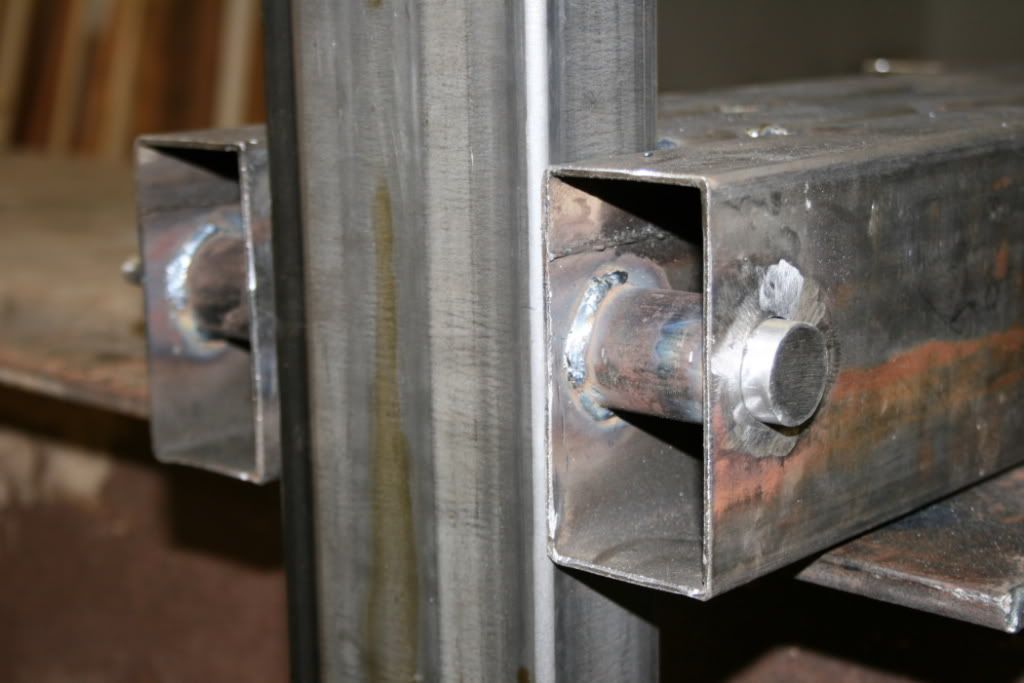
The press cavity is 16" when raised, allowing for easy insertion of the lay-up.
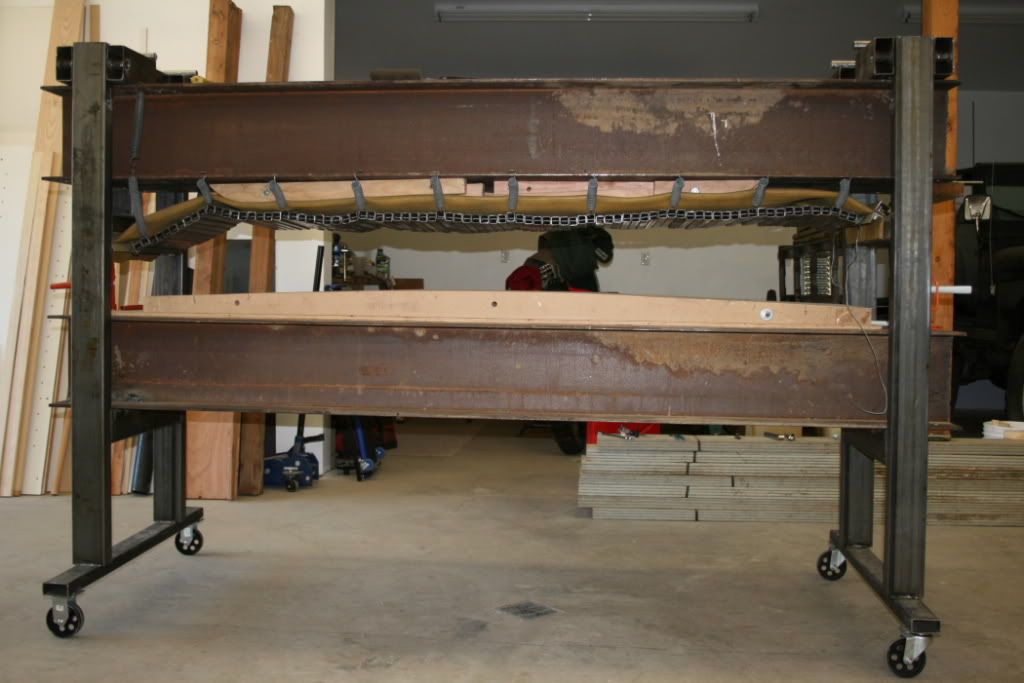
The press in the lowered positon. The cavity height is 12". I want to build a larger (taller) mold or shim it up.
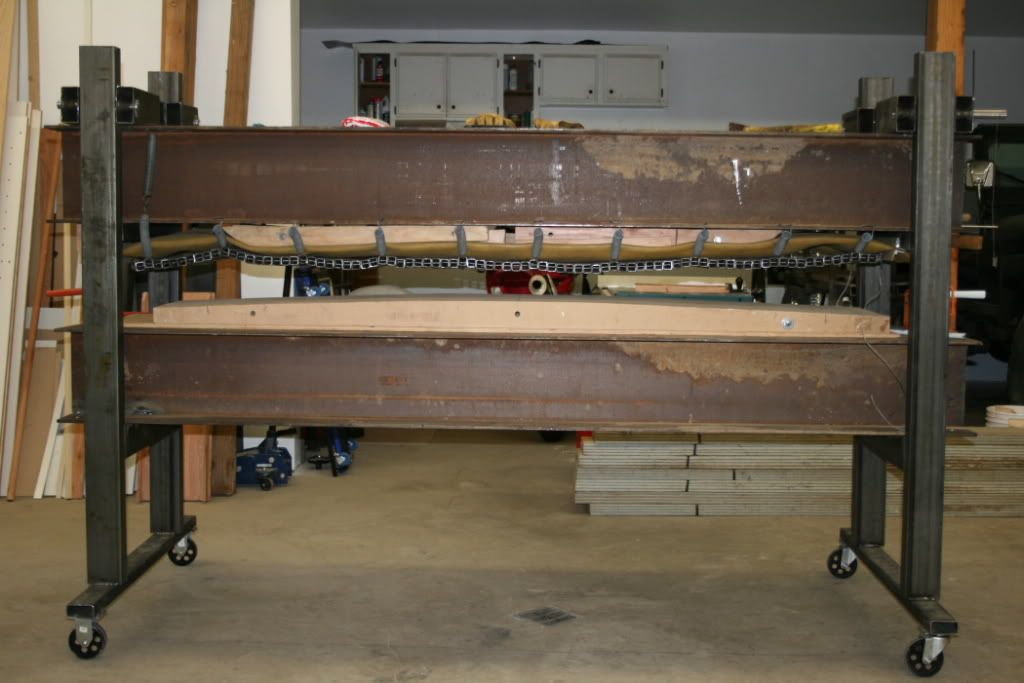
Here is the press under pressure. Started at 10psi and went all the way up to 86psi and held for three hours with no problems or leaks.
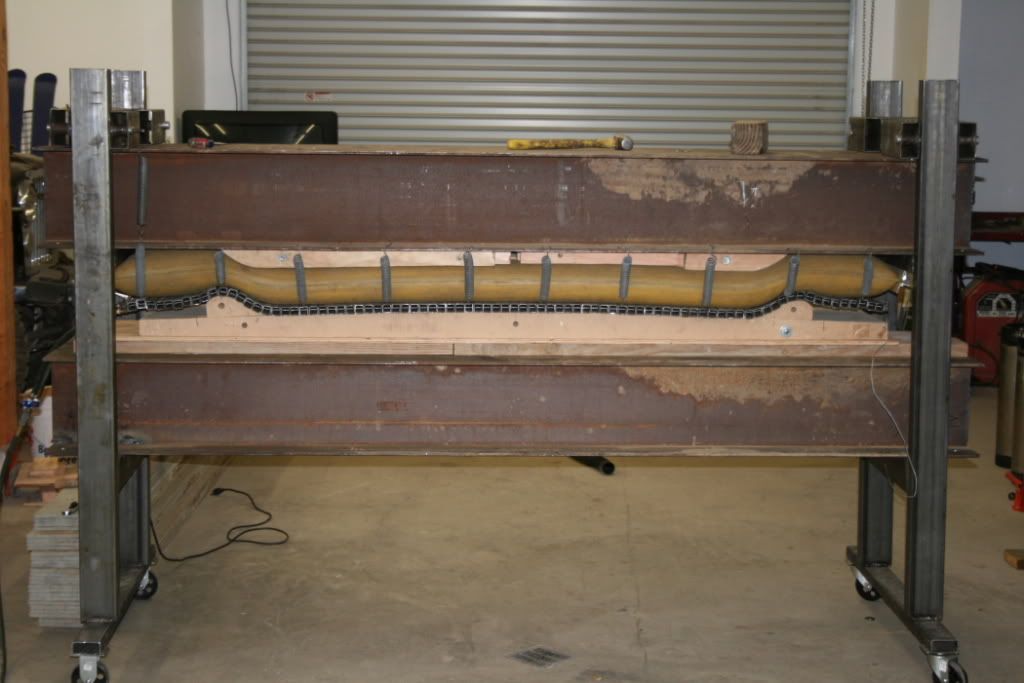
Side view...
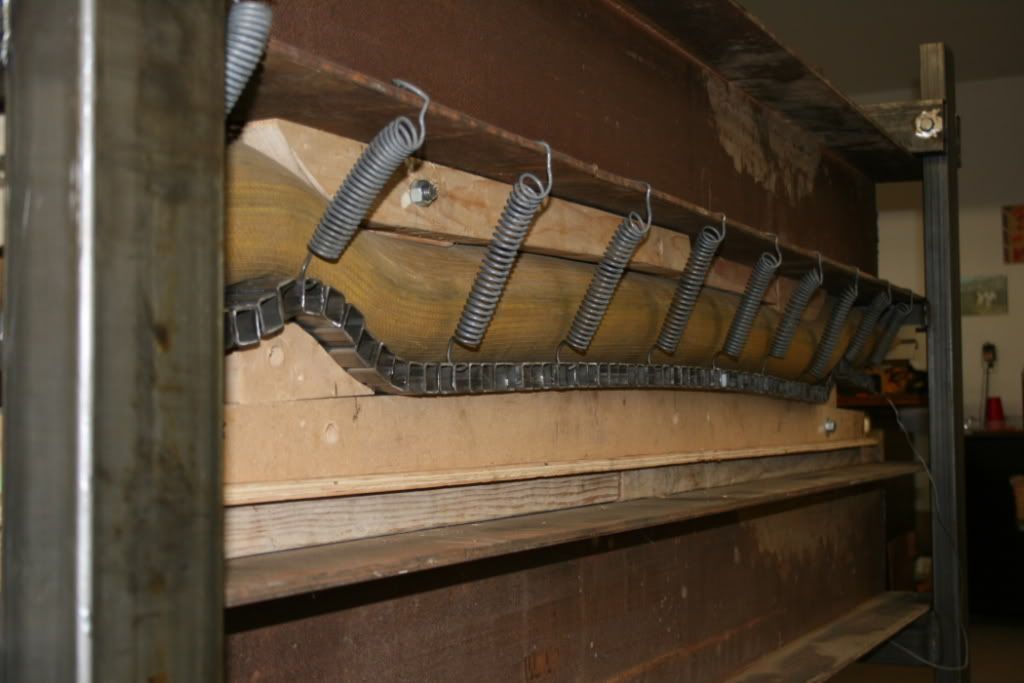
The next project is to build a new top mold that is adjustable. This should take up some of the space.
rockaukum