Page 1 of 2
Adjustable molds - 90 degree slotted system
Posted: Wed Nov 13, 2013 12:56 pm
by climberman
Thanks to goz for some inspiration and discussion at his place last week. I think I have my press layout in my head now.
I want to have an adjustable mold setup to minimise the need to get external CNC work done.
chrismp and the balkan snowboards folks have a 90 degree slotted setup - like the pic below. I'm seriously considering this style. Any comments, recommendations, advice as to yes or no with this style?
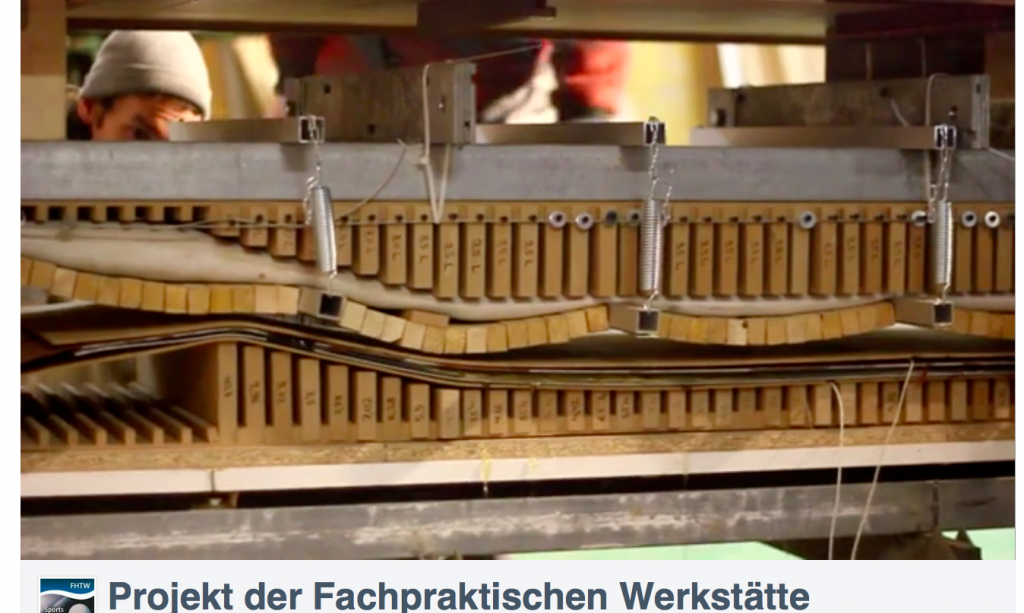
[/img]
Posted: Wed Nov 13, 2013 4:41 pm
by EricW
Always more than one way to skin a cat. If you like it and it works, go for it.
Posted: Wed Nov 13, 2013 6:57 pm
by gozaimaas
Does that honestly come out smooth?
Posted: Thu Nov 14, 2013 12:10 am
by chrismp
Yes, boards come out perfectly fine! The 5mm hardboard and the 2mm aluminum cassette even out the gaps perfectly. I have a collection of mdf pieces with different heights, so I can make any type of mold I can think of (except for 3d molds) within a couple of minutes. I got the idea from artski first, and a few others have picked it up since. The only struggle we had was keeping the top mold pieces in place. This is now achieved by screwing small hooks into the mdf pieces and hooking them up to a steel wire that is fastened to the side of the press (the line beneath the black screws in the top mold). In the photo we used screws, but we've switched to using hooks since. The hooks look like this:

Posted: Thu Nov 14, 2013 12:57 am
by climberman
Thanks for the reply chrismp.
I take it you glued and screwed the mould separators that the vertical components slot into to a sheet of 5mm MDF?
Thanks for the hook advice, I guessed that's what the screws were for. Nice solution.
I will look for artski's as well.
Posted: Thu Nov 14, 2013 3:42 am
by chrismp
We actually took a 24mm thick board of laminated beech and used our cnc router to cut the recesses for the mold pieces. But glue and screws works as well i guess...just make sure to pre drill the holes in the separators so they don't split.
Btw, we tension the steel wire with turnbuckles.
Posted: Thu Nov 14, 2013 3:46 am
by PTTR
This is how we do it. It works and is easy to change.
We use 1mm cardboard to build up camber or rocker, the arrow, (if we want alot we throw some 3mm hdf in there aswell)
The top mold are blocks of plywood that slide on the black metal thing.
With two different tip and tail molds, one rocker, one plain, and chims (cardboard) we can get most forms and change inbetween kidskis, powderskis and snowboards.

Posted: Thu Nov 14, 2013 12:29 pm
by climberman
thanks chrismp and PTTR, very much appreciated.
PTTR, nice use of the cardboard. From the picture your tip and tail mold up top is ay 90 degrees to the press? And the ply is a bulk filler, which can have a form if need be or simply flat
Posted: Sat Nov 16, 2013 1:56 pm
by PTTR
Hmm. Don't really understand your question, but I can take a better pic on Monday when I will be back at the shop.
Posted: Sat Nov 16, 2013 8:06 pm
by ProbsMagobs
this idea really caught my interest but i have a vacuum press. So I kinda took the idea and ran with it. Its a cross between the boardcrafter press and this one. Let me know what you guys think. Should cost somewhere around $120-200 depending on how its done. In the end it will have a 3/16 sheet of hardboard on top with some sort of plastic or aluminum sheet on top of that. the threaded rod on the sides push the hardboard and aluminum into the shape of the camber. a vacuum film is placed on top of the aluminum sheet to press the board/skis. Should be able to be adjusted to boards/skis up to 200cm and can press 2 skinny boards at a time or 4 skinny skis at a time as its 2 feet wide
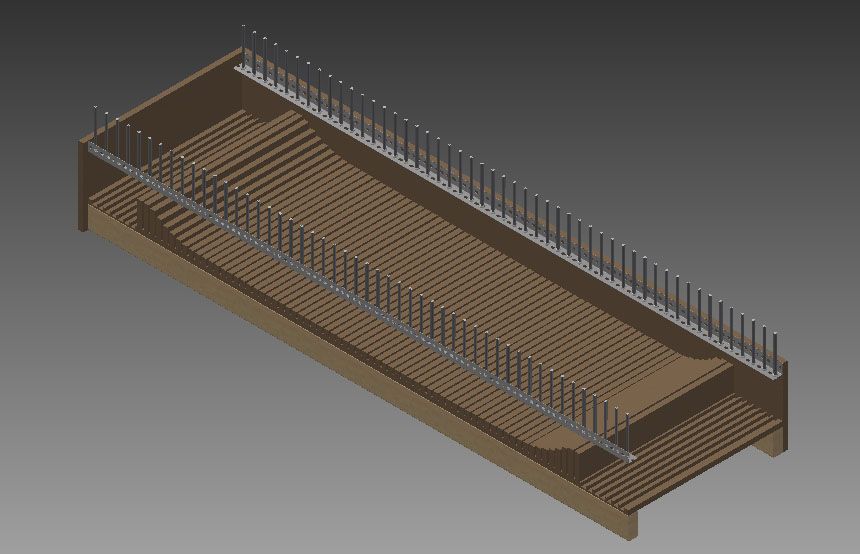
Posted: Tue Mar 01, 2016 2:51 am
by Minga
I know the topic is quite old but i got some question nevertheless

I like the idea and design of this adjustable mold but there is one thing i m wondering about.
What is the difference in height of the different spacers you have?. Is 1mm fine enough to build a smooth mold? It seems like you need an endless amount of them. Even with 1mm I would estimate you need about a 1000 of spacers to build different molds from rocker to flat rocker and camber. And i got the feeling that 1 mm is way to coarse.
cheers,
Hannes
Re: Adjustable molds - 90 degree slotted system
Posted: Fri Dec 24, 2021 10:31 am
by Jonrezz
Hanners I know it’s 5 years after you asked for clarifications but here was my approach:
I use a similar system as him but on a vacuum table and I use 1/2mm steps in height. I think 1mm would be too course. In total I have around 200 “height blocks” and it covers most configurations, I just make more as I need them. Usually I’ll have to cut 5-10 new height blocks to accommodate a new shape - each shape uses around 40 height blocks depending on ski length. I also made a few sets of tip and tail ramps - early rise, steep, shallow. the spacers sit on a rack that collapses and when you put the height blocks in into the overlapping section of the racks it locks the length in place. the tip/tail spacers are attached with 10-24 threaded rods:
Here’s the original concept:
I revised it so that it collapses on itself and the spare rack length isn’t poking into the silicone sheet under vacuum:
Some build/action shots:

Re: Adjustable molds - 90 degree slotted system
Posted: Wed Feb 23, 2022 6:51 am
by snowbo
why so complicated when it comes to vaccuum pressing.
for 2-D Molds this easy solution is suitable - just use a medium flexible plate, put your nose and tail blocks on and for the camber/rocker profile just clamp this to a stable surface.
so you can adjust the place of the rocker withour andy fixed grid - just place a suitable stick under the plate...
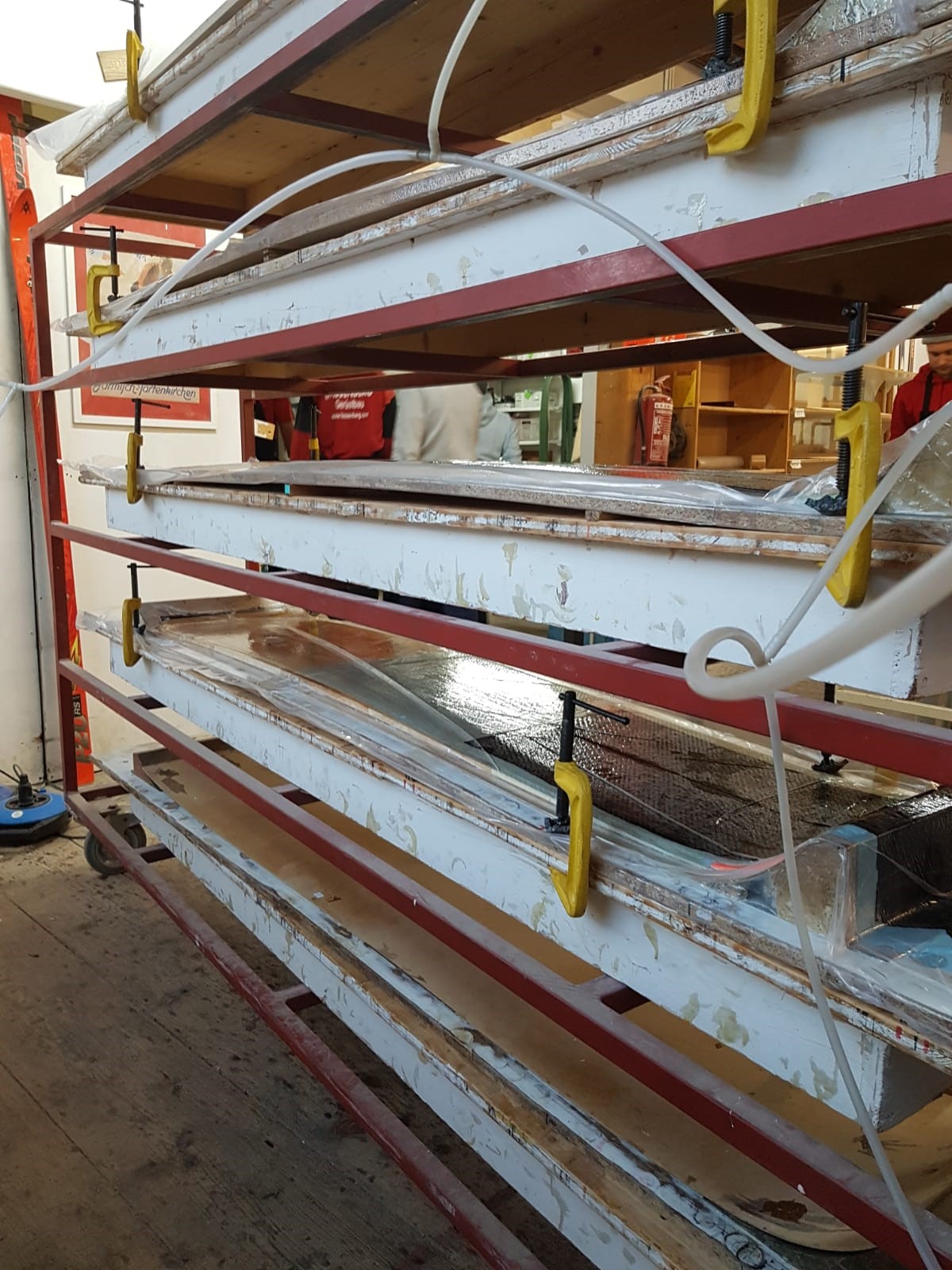
- vac-press adjustable01.jpg (355.38 KiB) Viewed 3862 times
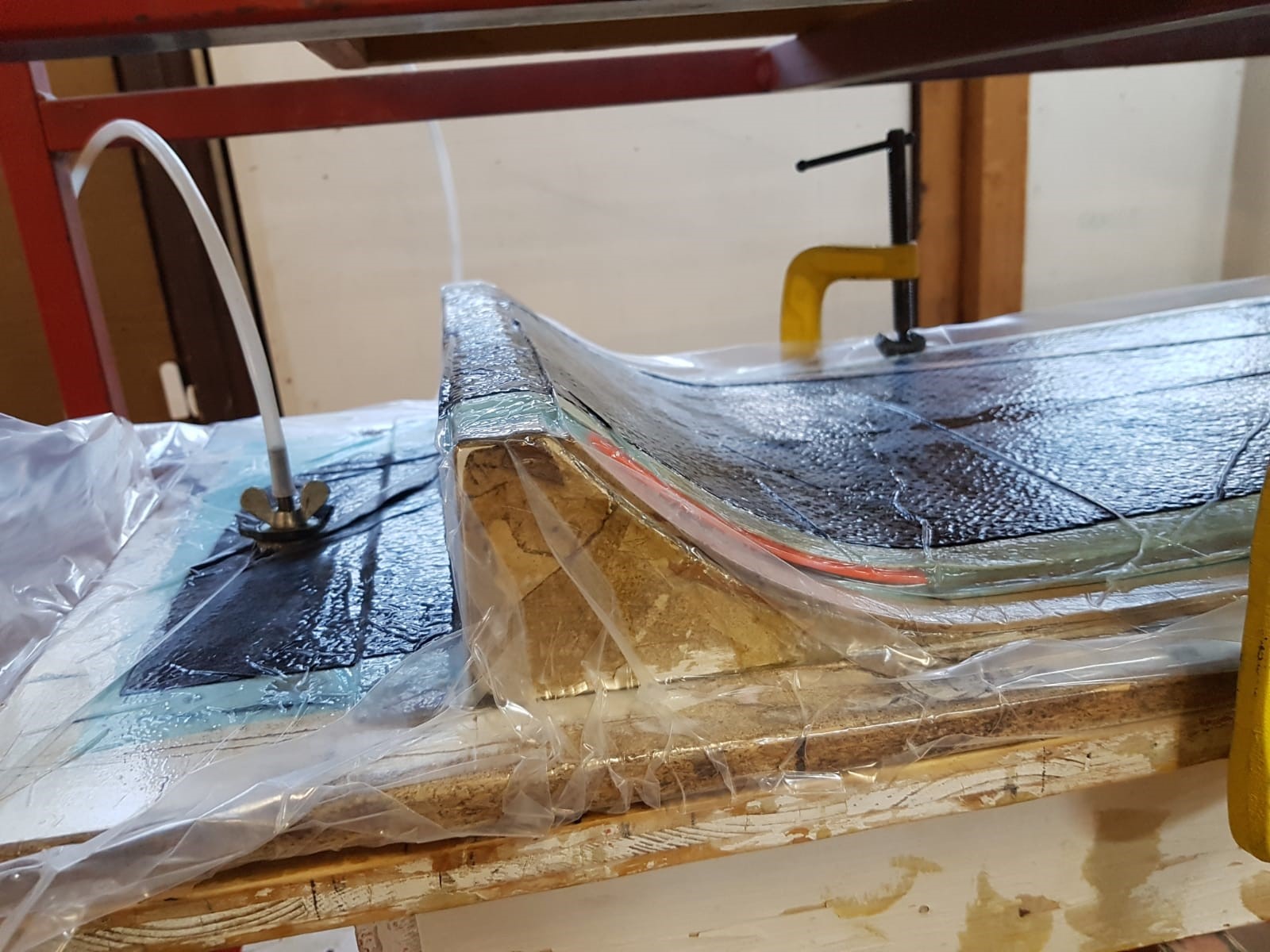
- vac-press adjustable02.jpg (299.77 KiB) Viewed 3862 times
Re: Adjustable molds - 90 degree slotted system
Posted: Mon Mar 25, 2024 6:29 am
by seb g
Hello,
after several years of use in a vacuum bag my current form is starting to age badly. So I'm going to make a vacuum table and I find Jozerr's system very ingenious, I only wonder if when unmoulding the sole is smooth or if there are slight waves on each support point.
I thank in advance users of this type of system who can give me feedback.
sorry for my english i'm french and i use google translate!
Re: Adjustable molds - 90 degree slotted system
Posted: Wed Apr 03, 2024 3:22 am
by chrismp
With a vacuum setup there probably won't be any imprints from the mold as the pressure is pretty low.
PS: for translations deepl.com often works better than google
