Page 5 of 6
Posted: Wed Feb 27, 2013 9:29 pm
by falls
I get the ski out of the press having placed skim coat of epoxy on top of veneer during pressing. Sand back to smooth and apply 2-3 coats of clear coat (water based exterior polyurethane)
http://www.bunnings.com.au/products_pro ... e=products
I think doing some clear coat layers first stops the ink bleeding under the vinyl stencil when you are applying to raw veneer.
I sand back the second clear coat with 400 grit and stick on the vinyl stencil. Paint on the epoxy screen printing ink with a brush (it is gloss finish, brush strokes don't seem a great problem and perhaps add to a hand done look?).
I use an ink from australian specialty inks but I assume the nazdar inks would be similar (
http://www.austspecialtyinks.com.au/index.html - the two can epoxy on that link).
It is air dry in 2 hours. I usually leave overnight before peeling the vinyl stencil, but think this would be OK at 2 hours. I did the same with some oil paints once and peeling while the paint was still wet was difficult and didn't end well (especially if you have small pieces of vinyl you need to lift with an exacto blade to remove them).
I am not pressed for time so I probably tend to leave the skis alone for the whole period of epoxy curing like you would for screen printed plastics (4 days minimum). I don't do this intentionally it just happens that way by the time I get around to doing more clear coats.
I then spray on 2 more layers of the above exterior poly without abrading the epoxy ink at all. I think once 2 more coats are on you could sand lightly before a finish coat but I haven't ever been brave enough to sand over the decal in fear of sanding through and spreading black pigment about.
Posted: Sun Apr 14, 2013 4:05 am
by falls
Got another pair pressed this weekend.
A little worried about my current mold not really producing skis that are that flat. Seems to be producing a convex base underfoot then more or less flat at the tip/tail.
I pressed this pair without heat. Used a new epoxy from the sister company that supplies epoxy to Kingswood skis in NZ. It is a rubber toughened epoxy. Will see how it goes. With just one heat blanket I wasn't happy with the camber results I was getting from my mold so thought I would give the room temp cure a go again.
Hoping the convex bases aren't beyond resolution on the belt/stone.
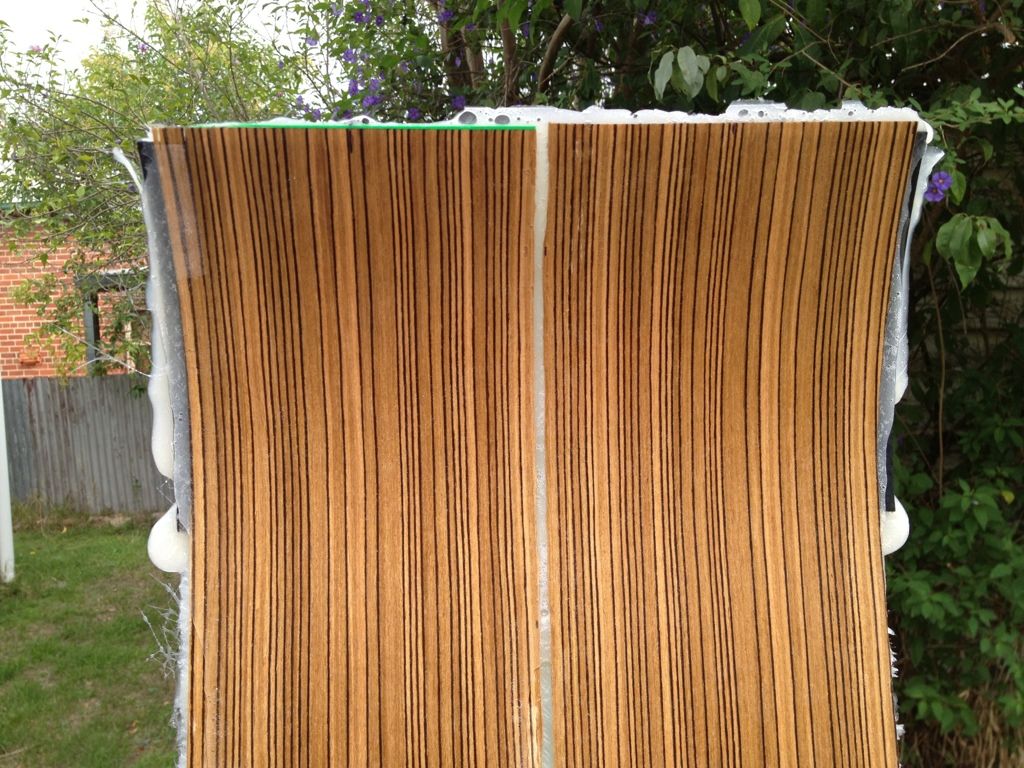
Posted: Sun Apr 14, 2013 4:15 am
by vinman
Is that black limbs veneer or zebra wood?
Posted: Sun Apr 14, 2013 5:03 am
by falls
It is a reconstituted veneer. Like zebra wood.
It is called zebu.
http://www.briggs.com.au/veneer_details.php?id=160
Posted: Sun Apr 14, 2013 5:25 am
by Richuk
Hey man!
The difference in thickness might be affecting the cure cycle, such that the lower laminate is cured to a greater degree.
Sounds like the tip section is sufficiently thin, so one heat mat is sufficient to heat right through and the cure cycle is uneffected.
With the core being thicker underfoot, the cure cycle for the upper laminate maybe 10 mins behind the lower laminate and or not reaching temp.
Is the cat-track open - acting as a heat sink?
Putting a thin piece of bamboo on the heat mat and heating it up to 80 degrees, is a good experiement and should help you fine turn any issues.
Posted: Sun Apr 14, 2013 6:59 am
by skidesmond
I like that veneer. I've used reconstituted teak, looks great and is affordable.
Posted: Mon Apr 15, 2013 3:49 am
by falls
Thanks guys.
Rich - unfortunately these were pressed without heat and the problem of convex base is still there. I usually heat from the top as well so if there is uneven heating it would be cooler on the bottom side.
Anyway I have pulled my bottom mold apart and hopefully will be able to sort things out.
On the plus side I also just received a new 1/2 inch plunge router in the mail today
I am frustrated that getting the mold ribs done by CNC isn't precise enough to have a flat mold (in my experience anyway). Once they are all bolted together there needs to be some sanding to "flatten" things out. Then you need to have it all sitting on an absolutely flat surface when you sand it otherwise you are doing more harm than good. The other trouble I seem to have is that when you bolt the pieces together the ribs don't always sit down flat against the table top either so what you think is flat isn't once the pressure is applied. I am wondering if applying a hardboard skin to the mold evens minor things out (plus a few aluminium skins and a heat blanket).
Any tips on getting a cambered mold flat? I wondered also about making the ribs out of plywood instead of MDF.
Posted: Mon Apr 15, 2013 5:13 am
by Richuk
OK.
Are you sure the cat-track isn't rolling over the top of the skis and creating pressure points across this narrow section?
Posted: Mon Apr 15, 2013 6:00 am
by threeninethree
I thought the same thing about my cnc'd molds. Before I even took the chance I put a 1/4" AL plate on top of the bottom mold. (See Headmonkeys press).
No concave/convex issues at all.
Posted: Mon Apr 15, 2013 8:36 am
by MontuckyMadman
If your cnced ribs are not within a fraction of a mm then you need to find a new cnc guy.
They should be good to g from the shop with some al on top. I duuno that 1/4 is nessesary but you do need something. then with the heat blanket betweeen 2 pieces of al and the cassettte, sh-it should be super flat
Posted: Mon Apr 15, 2013 10:37 am
by vinman
I've been thinking of trying to use a laser lever to shoot a beam across my mold surface so I can fine tune it with sanding and spackle to flatten it. But my stuff is coming out really well do I may not try to fix what isn't broken.
Posted: Mon Apr 15, 2013 3:29 pm
by MadRussian
falls wrote:
Any tips on getting a cambered mold flat? I wondered also about making the ribs out of plywood instead of MDF.
how about using profiler to create camber mold. in other words bolt together MDF ribs then profile camber. This way it should be flat. This is just an idea which should work
Posted: Tue Apr 16, 2013 3:29 am
by falls
Thanks all.
I think I need a good CNC guy that understands how precise I need things to be.
Montucky: are you saying you cover your MDF mold with a thick sheet of aluminium before your heat blanket that is sandwiched between two thinner sheets of aluminium? How thick? No sanding? And how do you bend it to the shape of your mold?
Posted: Tue Apr 16, 2013 7:49 am
by MontuckyMadman
U know about anealling right or detempering? Not too thick. Think we went .050 inches
All the same as our cassettes. And yes too all.
Posted: Tue Apr 16, 2013 3:03 pm
by falls
Do you bend it by hand or have access to a pyramid type roller?
Thanks for the input.