Page 1 of 3
New base mold idea
Posted: Tue Oct 19, 2010 5:46 pm
by COsurfer
I don't know if anyone has posted this idea but I haven't seen it so I thought I would put it out there for comments. I have to give Jekul full credit for this design. I just have the CNC machine to make it work. It’s a new way of creating a base mold by CNC'ing the top of MDF planks. Jekul bought 1-1/4" MDF that we CNC'd. I just glued two 3/4" MDF's and it seems to work just fine. Here are a few pics:
The CNC'd piece will be cut at both ends and placed on a 2x4 base. We will CNC tip and tail risers that will bolt to the ends of this CNC'd plank. The CNC plank can be interchanged with different shapes.
These specific pictures are the base for a snowboard with rocker and camber. Similar to Lib-tech's TRS series:
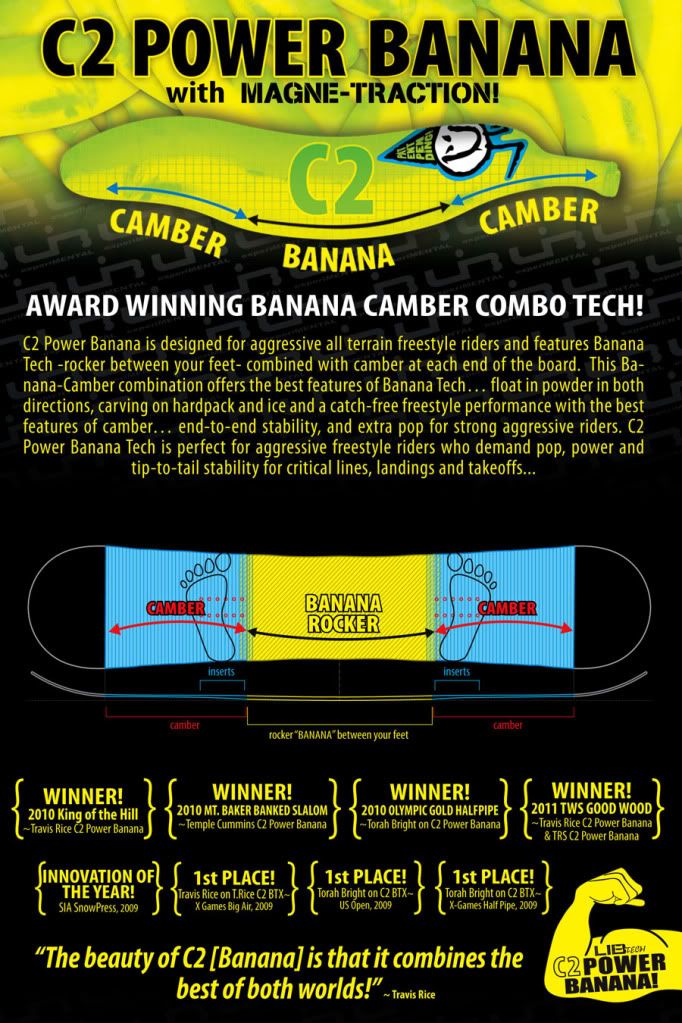
Posted: Tue Oct 19, 2010 6:01 pm
by doughboyshredder
Sorry to be the bearer of bad news, but it probably won't work.
I use 1/2" particle board as the pressing surface between my tip and tail molds. It's sitting on the steel camber plate that I use. I have been real surprised that the particle board stays flat through a few press cycles even with the high heat and pressure that it's subjected to.
I thought for sure that mdf would be more stable. Surprisingly it wasn't. I used a 3/4" sheet as my tip and tail blocks were a bit thicker for that board. After 2 pressings the mdf was warped. Flatness gone. No longer usable. There was a visible impression of the board on the mdf sheet. At least a 1/2 mm maybe more of indentation. My guess is that it has something to do with the glue that they use to fabricate it not standing up to heat. So, if you're not going to use heat, you may be fine. I was shocked that the particle board withstood the forces in that orientation much better than the mdf.
Posted: Tue Oct 19, 2010 6:13 pm
by MontuckyMadman
good idea. Sounds like particle board over your new mold and some al sheet to boot.

Posted: Tue Oct 19, 2010 6:16 pm
by COsurfer
I am a little confused. I know you have a metal camber plate but most people use MDF orientated in the vertical direction with no problems, including myself. I use a 1/8" mdf from tip to tail on top of my ribs with no impression of my board on the 1/8" MDF or the 3/4" molds. This new orientation will more evenly distribute the force since we have virtually eliminated any inconsistencies on the press face.
Posted: Tue Oct 19, 2010 6:35 pm
by MontuckyMadman
Yeah I was thinking, ig uses mdf and heat with no warping. YMMV apparently.
need more al sheet?
maybe your problem, dbs, is the steel not the mdf?
build up of heat?
Posted: Tue Oct 19, 2010 6:41 pm
by sammer
Sounds like dbs is on to a new cassette making process.
Press a dozen boards in the same spot and instant cassette.
sam
Posted: Tue Oct 19, 2010 7:29 pm
by doughboyshredder
might be the high pressure I am using (80psi at the laminate). Maybe I had a bad batch of mdf. Not sure. I don't have any issue with the vertical oriented mdf in the tip and tail blocks. OH, and my aluminum is only .120 then blanket then .120 then .120 for the cassette sheet. Imprint of board is making it through all of that and in to the mdf.
Posted: Wed Oct 20, 2010 8:54 am
by rockaukum
Dough,
Why are you pressing at 80psi? Seems high and others are having great success at lower pressures. Is it a reduced weight?
ra
Posted: Wed Oct 20, 2010 9:16 am
by doughboyshredder
rockaukum wrote:Dough,
Why are you pressing at 80psi? Seems high and others are having great success at lower pressures. Is it a reduced weight?
ra
Yep. Reduced weight. Squeezes out any and all excess resin. Also helps with air bubbles as far as I know. First got the idea for such high pressure from Never Summer, as I was told that is what they press at.
Posted: Wed Oct 20, 2010 1:50 pm
by MontuckyMadman
A guy from TGR tried to ethug me on some 333 shit over pm and he told me the guys he shares a warehouse space in denver press at 120 psi. I told him BS and then we really got into it.
Posted: Wed Oct 20, 2010 2:22 pm
by OnDeck
MontuckyMadman wrote:A guy from TGR tried to ethug me on some 333 shit over pm and he told me the guys he shares a warehouse space in denver press at 120 psi. I told him BS and then we really got into it.
Sounds like bullshit to me, too. Even 80 sounds high, but if people are getting away with it then best of luck!
Posted: Wed Oct 20, 2010 2:28 pm
by Richuk
... isn't there a glass to epoxy ratio to aim towards?
Posted: Wed Oct 20, 2010 3:18 pm
by doughboyshredder
MontuckyMadman wrote:A guy from TGR tried to ethug me on some 333 shit over pm and he told me the guys he shares a warehouse space in denver press at 120 psi. I told him BS and then we really got into it.
At the air bag or at the laminate? Depending on the sf of the laminate and air bag they may be inflating to 120 and getting a lower psi at the laminate.
Depending on how much space the air bag has to inflate in to the contact patch may be pretty small. That's one of the reasons I designed my press so that I could raise the top for loading. I only have a couple inches for the hose to inflate in to therefore increasing the area of the surface patch.
Still, 120 seems high.
... isn't there a glass to epoxy ratio to aim towards?
my understanding is that there is not.
Some applications are at 75/25 some are at 25/75. A lot of people throw around 50/50. I think vac bagging produces more like 40/60 and most pneumatic presses 55/45 maybe 60/40. Would take a lot of building and weighing and testing to really nail such a detail out. My opinion has always been that as long as the fibers are saturated that less epoxy is better both for weight and strength.
Posted: Wed Oct 20, 2010 3:41 pm
by COsurfer
Either 80 psi or 120 psi is nuts if you ask me. I wouldn't trust my press at that pressure. I press at 50-60 psi.
Here is the final pic of my mold. I still need to add metal strips to attach the tip/tail spacers to the mid section:
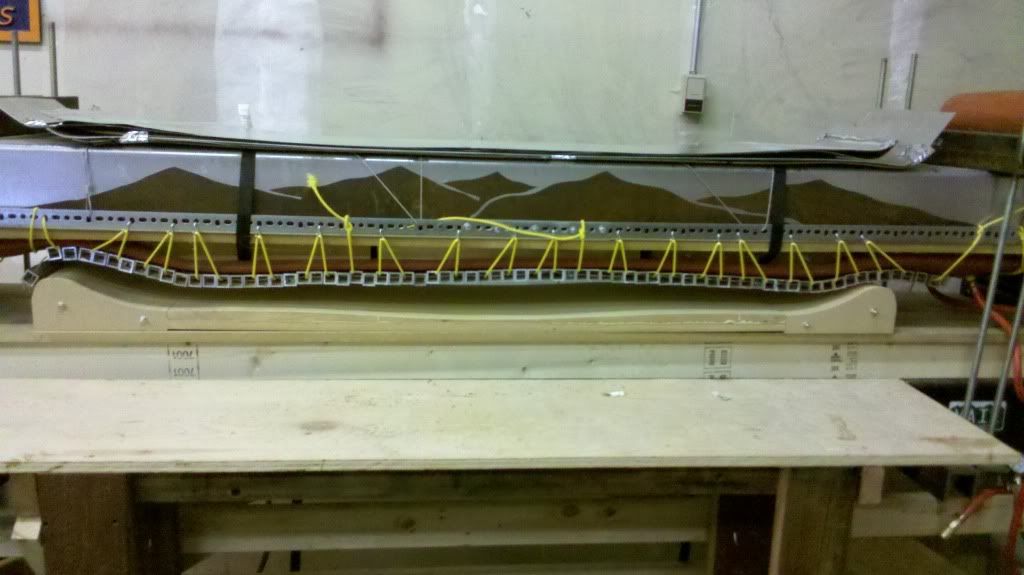
Posted: Wed Oct 20, 2010 5:31 pm
by doughboyshredder
COsurfer wrote:Either 80 psi or 120 psi is nuts if you ask me. I wouldn't trust my press at that pressure. I press at 50-60 psi.
Here is the final pic of my mold. I still need to add metal strips to attach the tip/tail spacers to the mid section:
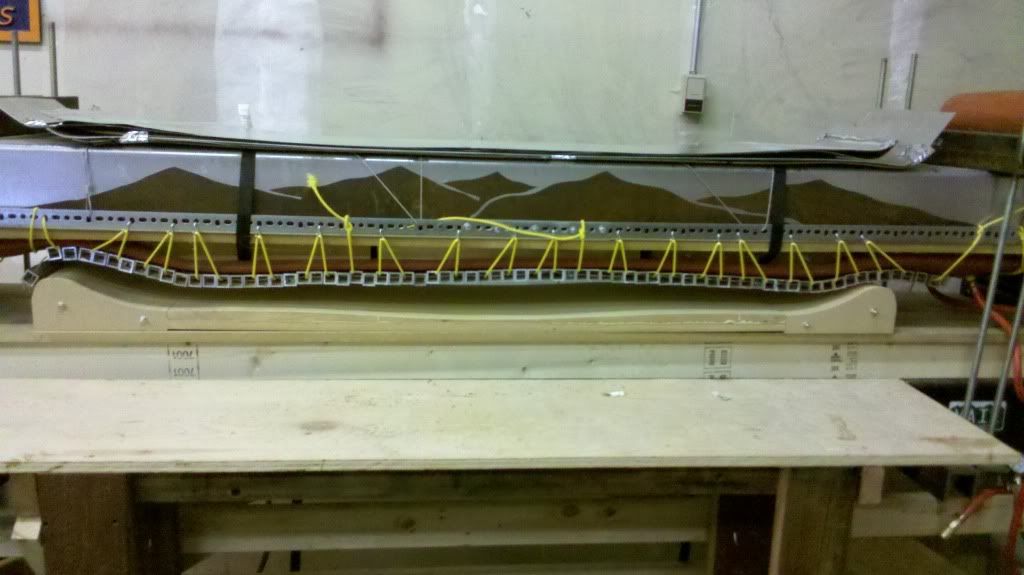
From the looks of it, you may get a lot less than that even, based on how much space there is for the airbags to inflate in to. What's your actual contact patch when fully inflated?
80 psi is completely unnecessary though. But, my boards are really light and have withstood significant abuse.
That mold looks great, btw.