Page 1 of 2
when i hook up cat-track
Posted: Fri Aug 15, 2008 3:16 pm
by knightsofnii
when I go to add my cat track to my press system:
What kind of stuff should I put between cat track and board top to ensure that I get uniform pressure on the nose and tail curve?
Cat track beams are square tubes and well, nose and tail are round.
Will an 1/8" thick piece of aluminum be enough? As Han Solo liked to say "I have a bad feeling about this"

Should I go for thicker?
Posted: Fri Aug 15, 2008 5:53 pm
by threeninethree
Are you getting a dead space in the transition to the tips and tails? Ive been thinking of using a sheet of aluminum and then a sheet of medium hard neoprene (3/8" thick) and a thiner sheet of aluminum to ensure full contact. I posed the question of how much unpressurized dead space to leave in one of my posts for that very reason. I'm sure I will be experimenting in the same problem in the next coming weeks.
Posted: Fri Aug 15, 2008 7:12 pm
by doughboyshredder
Pretty common problem.
One of the solutions I have seen was little miniature hydraulic rams added to both sides of the board at the tip and tail radius.
Another solution is to have a less radical angle to the tip and tail.
Another solution is to have shims for the tip and tail radius.
I wouldn't think any sort of neopren or any other material would be a good idea, because it would affect the pressure on the sidewalls of the board.
I have been curious about this aspect for a while. Hoping some of the more experienced builders will chime in.
Is this as much of an issue for skis as it is for snowboards?
Posted: Fri Aug 15, 2008 8:47 pm
by knightsofnii
i would imagine if your skis have tips and tails then it is the same issue if using cat track. I'm thinking that just making sure the steel beams are butted snug together, and using a thicker plate underneath like 3/16 to 1/4inch, and making sure both end right at the tip of nose/tail or the ends of the mold, so that they dont bend over and cause lift somewhere inside. I'm thinking that may be enough. I think some even go as far as welding or fastening the cat tracks to the plate underneath.
Can you describe the hydraulic rams, or shims solutions a little more? I cant picture them.
Posted: Sat Aug 16, 2008 8:20 am
by rockaukum
is this what you are talking about?
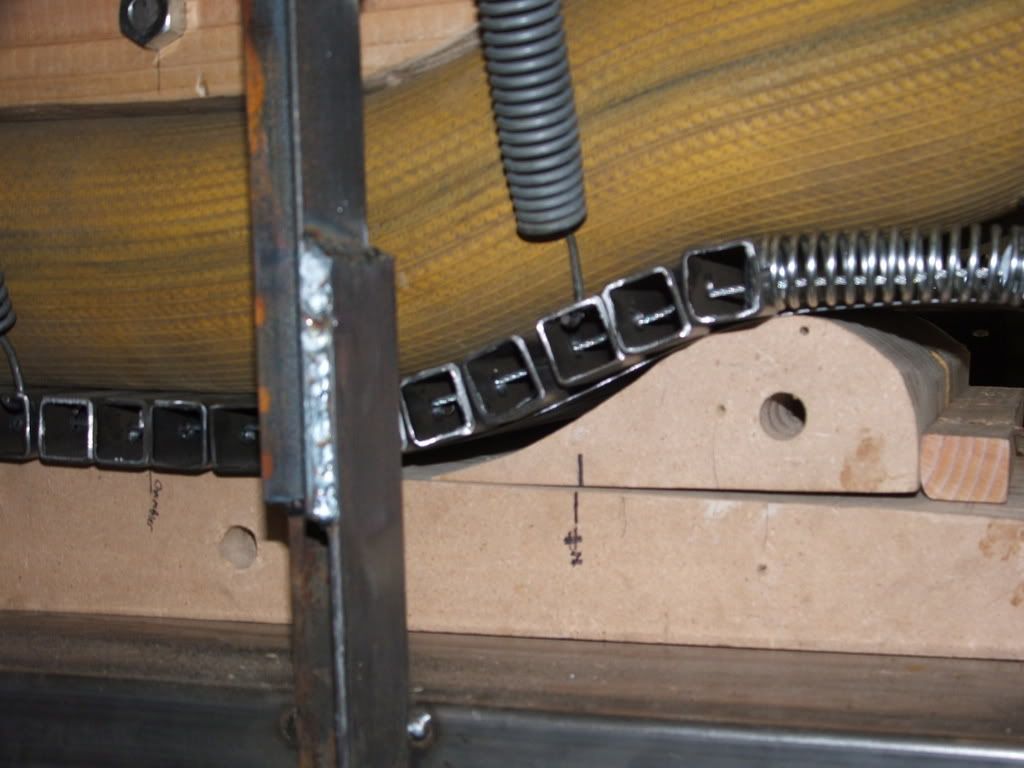
I went to tap plastics and got a piece of 1/8" HDPE. I put it above the final layer of the pressing then wrap in plastic to contain the epoxie. This seems to have solved my problem of this gap
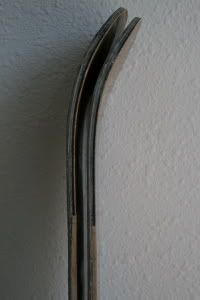
ALso make sure you have a good line up with the top mold in relation to the bottom mold.
If this is not what you are talking about .... Oh well....
rockaukum
Posted: Sat Aug 16, 2008 8:52 am
by knightsofnii
that's exactly what i'm talking about, but even after getting those bars to press down, they're flat so there's only contact POINTS and not a real contact SURFACE, that's why I'm wondering what kind of materials i should use over it.
But thanks for that photo because that's part of what I mean. I think ending your cat track right at the tip of that bottom mold will help solve that too, and getting a more pronounced top mold, and allowing the bag run-off to go UP instead of bent over the bottom mold.
our bag is 12" diameter, 18" wide at rest, its huge, it just goes everywhere so I have to figure out how to contain it, haha.
Posted: Sat Aug 16, 2008 9:01 am
by knightsofnii
rockaukum, also try decreasing your mold cavity, get the top mold closer to the bottom, that way the airbag is not inflating to its capacity before pushing everything down. I bet if you close that gap 2" or more you will have some improvement.
Posted: Sat Aug 16, 2008 1:01 pm
by rockaukum
I have solved my problem as stated. And yes shim above the mold (hose cat and all) to decrease the amount that the hose has to inflate resulting in more surface area contact of the hose has proven effective.
As far as the cat track in the tip and tail curve, the HDPE seems to carry those little spaces between the cross bars in the cat track with out any problems. That being said, I have no way of actually measuring the force in those areas. All I know is that the ski is smooth throughout the tip curve.
rockaulum
Posted: Mon Aug 18, 2008 3:32 am
by Kevin6q
It looks like the track is getting pinched/pinned by the hose as it inflates so it cannot move. As the hose inflates it pulls the track towards the tips. Other than ease of moving is there a reason for the cables? Use the cable over the center of the ski and lay in the rest of the tubes w/o the cable and i bet they remain flat to the layup.
Posted: Mon Aug 18, 2008 3:56 am
by hugocacola
hey knght , you just need some 1mm steel sheet and averithing perfect...
Posted: Mon Aug 18, 2008 1:21 pm
by knightsofnii
thanks hugo, and what kevin said makes perfect sense.
Posted: Sun Aug 31, 2008 5:51 pm
by hydrant71
knight,
i also use 1/8" hdpe in combination with with the cassette top. hdpe on top of board then cassette when pressing boards with no topsheets,
smooth as glass.
Posted: Mon Sep 01, 2008 9:25 am
by rockaukum
Hydrant,
What release agent do you use on the HDPE? I used a car wax but was wondering if there is something else I should be looking at..
rockaukum
Posted: Mon Sep 01, 2008 9:40 am
by knightsofnii
if its super smooth you can probably get away without release agent
Posted: Mon Sep 01, 2008 2:19 pm
by iggyskier
rockaukum wrote:Hydrant,
What release agent do you use on the HDPE? I used a car wax but was wondering if there is something else I should be looking at..
rockaukum
I use hdpe with no release agent when doing wood veneers with no issues at all. just clean it once over before reusing.