Page 8 of 9
Posted: Tue Dec 20, 2011 12:24 pm
by sammer
The majority of the skis I have built usually have a sidecut setback between 50-65mm.
65mm being the most common.
When I was designing my first pair I figured with my ball of foot at the center of the running length I wanted the narrowest part of the ski at boot center.
So measured my boot and came up with 65mm.
Not really sure if this is the "approved method" but so far has worked.
sam
Posted: Tue Dec 20, 2011 2:55 pm
by Richuk
I was looking at the Voile site the other night, you might want to check out what they are doing and see if there are any similarities. Perhaps they would be prepared to talk about their mounting position ... bit cheeky, but sits under the heading of market research???
Posted: Tue Dec 20, 2011 4:33 pm
by ben_mtl
I just had a look and their profile sheets are interesting... the ski I'm working is really similar to the Charger except I have more tail rocker... but the top view is amazingly close !
Posted: Wed Dec 21, 2011 4:58 am
by ben_mtl
Now I've settled for a binding position I have another dumb question...
I use to do full tipspacer tips and tails, like most of us I think. For this pair I wanted to try having wood in the tips with only a 20mm strip of tipspacer material around them. I did that on my first pair of skis and it was Ok but this time the tips are much more elongated so the thickness of the tip part of the core is not constant.
I made an hi-tech technical drawing to show you what I mean :
I don't want to have a thickness of 2mm over the first (and last) 25cm of the ski so I'm thinking of a way to compensate for the difference between core and tipspacer thickness in the "transition" area.
Maybe if I add a few layers of fiberglass over the tipspacer only in this area it could work ! I would need to overlap them in a kind of wedge fashion. (I hope it’s understandable, I don’t know how to explain it in English…)
The thing is I would have to know roughly how thick is a layer of fiberglass (pressed and cured) so I can put the right number of layers… Any info/guideline on that for 22Oz Triax ?
I still don’t know how much thickness I’ll have to compensate for at the thickest but it should be around 1 or 1.5 mm, I’ll know more about it tonight after I’ve profiled the cores.
Posted: Wed Dec 21, 2011 5:22 am
by vinman
I make my tips this way but use 25mm of tip spacer. I've found you need to make the thickness of the wood equal to the thickness of the tip spacer or you'll get a base that is not flat.
To do this I first plane my cores out and then use a sander to finish off the wood in the tip so that it matches the thickness of the spacer. This gives me a
Nice flat tip without having to worry about using the planer on that really thin section.
Posted: Wed Dec 21, 2011 5:47 am
by ben_mtl
All right I see, I could profile my core as I wanted but then sand the tips down to 2mm.
On my drawing that would mean the core to be 2mm thick from the tip end (far right) to the second dotted line from the right...
Then I would have a step which can easily be filled by fiberglass running full width of the core...
Is that what you meant ?
It's going to be quite a large step to fill, won't this add a lot of weight ?
Posted: Wed Dec 21, 2011 5:51 am
by vinman
No I just make the last maybe 1-2 cm of the core match the tip spacer thickness as well. This gives a smooth transition to the spacer and I don't have to add any material.
Posted: Wed Dec 21, 2011 6:06 am
by ben_mtl
OK but then in my case the 25cm that are the tip are gonna be 2mm thick ? That's what I wanted to avoid, I'd like to have the taper of the core thickness go up to maybe 10cm from the tip.
I made a 2nd drawing that shows your proposition (if I understood correctly) and what I'd like to achieve.
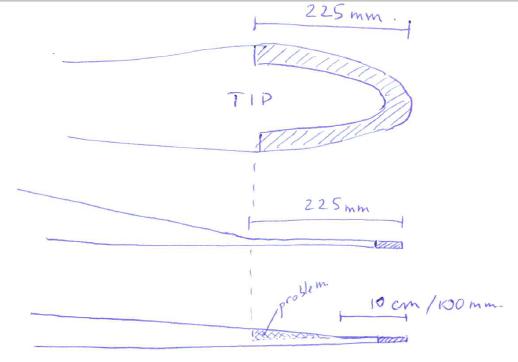
Posted: Wed Dec 21, 2011 6:34 am
by vinman
Ok I see what you are saying. Why not just do a shooter tip spacer area. That way you got more core and sidewall reaching into that zone that you don't want to be so thin. Maybe only 10 - 15 cm of tip spacer instead of 25cm?
Posted: Wed Dec 21, 2011 6:43 am
by ben_mtl
Yes that would be a nice solution but I see 2 issues :
- my core blank is already cut with sidewalls attached... that's not such a huge issue as I might be able to make a new core quite fast..
- I don't know if I'm gonna be able to conform the maple sidewall (it's a 3/4" wide strip) in those areas... I'll check what I can do tonight.
Posted: Wed Dec 21, 2011 7:39 am
by vinman
In that case maybe some light biax glass in the transition zone to help smooth things out or maybe some biax and some veneer to crate a taper?
But overall I think less top spacer on future builds will help solve your problem
Posted: Wed Dec 21, 2011 8:47 am
by ben_mtl
Actually I'm having a new template machined to correct that :p, hopefully I can run some tests tonight
Posted: Wed Dec 21, 2011 1:04 pm
by Jibber
Why not use a second layer of tip spacer and taper it (together with the core)?
Cheers, Christoph
Posted: Wed Dec 21, 2011 2:42 pm
by Richuk
Before you shape the core, you could rebate the tips and insert/bond on the tipspacer. If you're planning the core - you might want to be a little more conservative with the thickness - reduce it to 1.8mm and allow 0.2mm core material to remain.
Tricky though ...
Posted: Thu Dec 22, 2011 4:24 am
by ben_mtl
Jibber wrote:Why not use a second layer of tip spacer and taper it (together with the core)?
Cheers, Christoph
If I put 2 layers of tipspacer and taper it, the top surface won't be abraded and flame treated anymore. I don't want to mess with that for now. I'm a bit rush with this pair so I don't want to lose any more time dialing the surface treatment of the tipspacer. But I have to admit that's a perfectly legit idea, just not for me right now !
Richuk -» great idea too, I'll give that a try in the future !
For now as I said I'll go with a new template to only have 10cm of tipspacer in the tips. Only thing, yesterday I was so much in a rush (at work and at home later in the day) I messed up with my CAD software, didn't double check my work and when I went to get the template it was too large... I don't know what happened but a scale factor appeared somewhere and my template is like 6% bigger than it should be... measure once, cut twice you said ?