
Living-room project... CNC !
Moderators: Head Monkey, kelvin, bigKam, skidesmond, chrismp
-
- Posts: 2207
- Joined: Tue Mar 07, 2006 8:25 pm
- Location: Kenmore, Wa USA
-
- Posts: 2207
- Joined: Tue Mar 07, 2006 8:25 pm
- Location: Kenmore, Wa USA
I know what you mean Twizz, when we bought the house last year I had a few "to have", one of them was a nice "large" detached garage or a price that would allow me to build one... the 2nd case happened so I spent my fist summer there building my workshop, it was an nice experience !
On the CNC : I received all my 8020 extrusions and "all" the hardware ... some of the screws ended up not being the right length (my fault) so I have to order some new ones...
The laser-cut part should be done by next week-end ! can't wait !
On the CNC : I received all my 8020 extrusions and "all" the hardware ... some of the screws ended up not being the right length (my fault) so I have to order some new ones...
The laser-cut part should be done by next week-end ! can't wait !
A bad day skiing is always better than a good one at work...
-
- Posts: 1148
- Joined: Tue Jan 08, 2008 6:02 am
- Location: NJ USA
- Contact:
I bought the extrusions from a local dealer (faztek.ca), it's the same as 8020 extrusions but it's cheaper and I saved the shipping costs. I selected the extrusions in their catalog and ordered only the lengths I needed + t-nuts. If I had to order again I would ask them to tap the holes (at the ends of each extrusion)...
Just got all the lasercut parts today... looking for a few hours of fun : tapping tenth of holes and assembling everything !
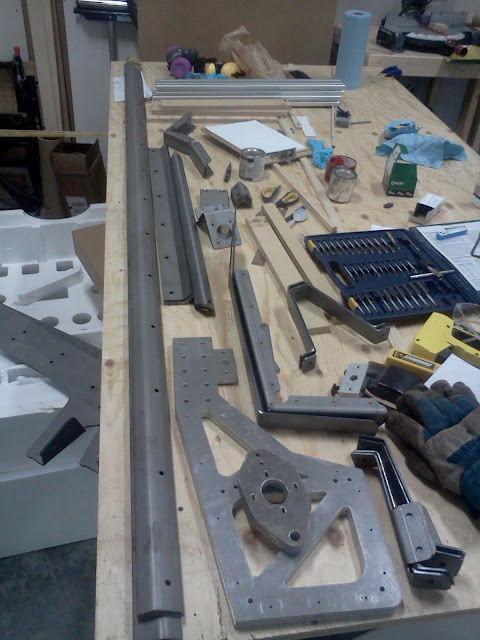
Total cost for the custom metal parts : 1000 CAN$... $400 of that is for the aluminum parts only (4 pieces).
I catched a couple mistakes I made on the parts (a few holes are too small, didn't account enough for the metal distorting while bending, things like that... nothing major but stupid rookie mistakes I could have avoided if I haven't been so excited..)
Just got all the lasercut parts today... looking for a few hours of fun : tapping tenth of holes and assembling everything !
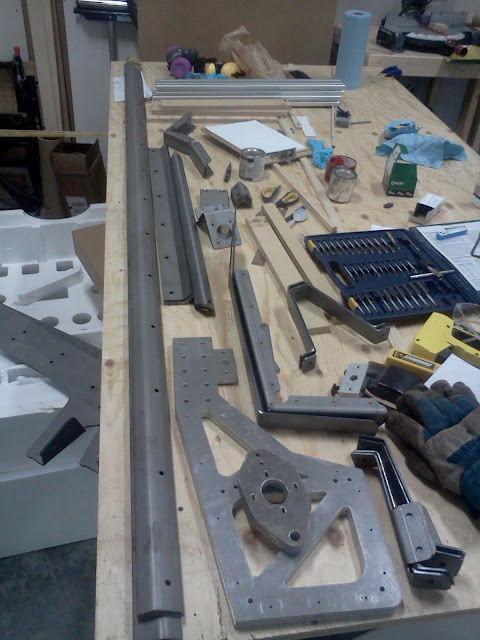
Total cost for the custom metal parts : 1000 CAN$... $400 of that is for the aluminum parts only (4 pieces).
I catched a couple mistakes I made on the parts (a few holes are too small, didn't account enough for the metal distorting while bending, things like that... nothing major but stupid rookie mistakes I could have avoided if I haven't been so excited..)
A bad day skiing is always better than a good one at work...
Gantry being assembled :
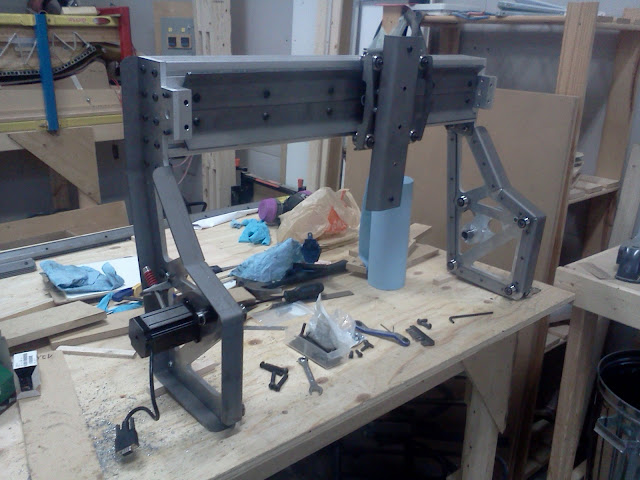
That's the time you realize Quality Control is not done for every customer... I had and sill have a lot of tuning to do on the parts. For now it's assembled but is not perfectly square... the Y rails are not parallel ( I tried briefly and understood it's not gonna be that easy...).
Anyway it's progressing and it's a lot of fun !
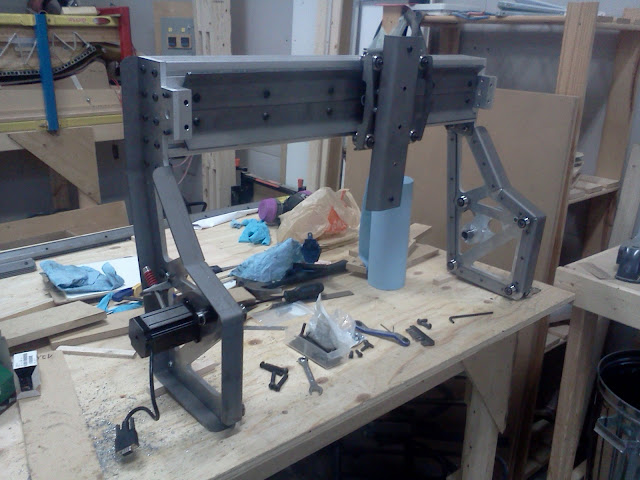
That's the time you realize Quality Control is not done for every customer... I had and sill have a lot of tuning to do on the parts. For now it's assembled but is not perfectly square... the Y rails are not parallel ( I tried briefly and understood it's not gonna be that easy...).
Anyway it's progressing and it's a lot of fun !
A bad day skiing is always better than a good one at work...
I tried to stay as low tech as possible to keep the cost down. Same thing for high-precision tolerances : it's way more expensive !
The rails are the critical point of my design, the 45 degree bend it the weak point in terms of tolerancing and precision. I'm gonna enlarge the holes used to fasten the rails to the 8020 extrusion so I can adjust everything a bit more.
If I don't manage to get something OK I'll have 2 options :
- Have another set of rails machined / bent, I would probably go with 1-piece rails (with the 2 bends on the same part) like for the Z axis, as opposed to the 2 rails you ca see for Y... I would set some pretty tight tolerances on those parts !
- Change the rails design and go with some other commercial option... that would require changing a lot of parts on the machine... that would suck !
You're right about the uprights : it some 3/8" aluminum + bent steel for rigidity. My problem here is that the big 8020 beam has not been cut 100% square... that also suck big time and I'm gonna have to make some kind of shims so the uprights are square to the beam... I contacted the seller to see if something can be done ( = new part) but I don't have high hopes for that...
The rails are the critical point of my design, the 45 degree bend it the weak point in terms of tolerancing and precision. I'm gonna enlarge the holes used to fasten the rails to the 8020 extrusion so I can adjust everything a bit more.
If I don't manage to get something OK I'll have 2 options :
- Have another set of rails machined / bent, I would probably go with 1-piece rails (with the 2 bends on the same part) like for the Z axis, as opposed to the 2 rails you ca see for Y... I would set some pretty tight tolerances on those parts !
- Change the rails design and go with some other commercial option... that would require changing a lot of parts on the machine... that would suck !
You're right about the uprights : it some 3/8" aluminum + bent steel for rigidity. My problem here is that the big 8020 beam has not been cut 100% square... that also suck big time and I'm gonna have to make some kind of shims so the uprights are square to the beam... I contacted the seller to see if something can be done ( = new part) but I don't have high hopes for that...
A bad day skiing is always better than a good one at work...
-
- Posts: 1148
- Joined: Tue Jan 08, 2008 6:02 am
- Location: NJ USA
- Contact:
i think any machine requires some "dowels" or shimming/adjusting to get it true when you get it assembled... i did a lot of research and checking forums etc and every single machine has its quirks to get it cutting perfect,
just get the thing together and operational... then work on the squaring of it all... sometimes the software can compensate for if say your machine is out a pinch, you can run a check to see how far out the cut is, and the software will make adjustments to compensate. no? Are you gonna use mach3?
just get the thing together and operational... then work on the squaring of it all... sometimes the software can compensate for if say your machine is out a pinch, you can run a check to see how far out the cut is, and the software will make adjustments to compensate. no? Are you gonna use mach3?
Doug
Yes I'm gonna be using Mach3... i didn't really investigate on software compensation for "non-true" axis but I believe some squareness problems can be fixed.
Regarding the 8020 beam I'm thinking about bringing the beam to a machine shop to have both ends surfaced on a mill... it would make it a bit shorter but it's easy to add a flat shim instead of a wedged one... plus I can just ask "OK make it "original length - 1/8" and put a piece of 1/8" sheetmetal as a shim... that would be easy :p
I'll keep on assembling and keep a list of what need to be addressed before I commit to any solution.
Regarding the 8020 beam I'm thinking about bringing the beam to a machine shop to have both ends surfaced on a mill... it would make it a bit shorter but it's easy to add a flat shim instead of a wedged one... plus I can just ask "OK make it "original length - 1/8" and put a piece of 1/8" sheetmetal as a shim... that would be easy :p
I'll keep on assembling and keep a list of what need to be addressed before I commit to any solution.
A bad day skiing is always better than a good one at work...
-
- Posts: 1148
- Joined: Tue Jan 08, 2008 6:02 am
- Location: NJ USA
- Contact:
-
- Posts: 2207
- Joined: Tue Mar 07, 2006 8:25 pm
- Location: Kenmore, Wa USA
the gantry is 32in wide for a 24in travel on the Y axis. I went with NEMA 23 steppers \ G540 controller for now as it was easier/cheaper and that's what was used on the machine I took as a reference. If I see the steppers are not strong enough, switching to NEMA 34 won't be a huge modification.knightsofnii wrote:how wide is that gantry? and what motors did you go with, nema23 or 34?
A bad day skiing is always better than a good one at work...