Page 2 of 2
Posted: Sat Nov 26, 2011 4:15 pm
by sammer
Wow RA, thanks for the pics.
Simplicity at its best!
sam
Posted: Sat Nov 26, 2011 7:41 pm
by Jekul
I've done something very similar using 3/4" MDF on top of my camber/rocker shims. Using a heated blanket at 175-F I can't detect any "steps" or shim marks along the way. I haven't gone beyond 10mm camber and 30mm rocker...yet.
Posted: Sun Nov 27, 2011 4:17 am
by Richuk
More detail is needed to define the factors which lead to success.
Failure certainly looks like this:
- 1.3mm AL
- 80 degrees
- 60 psi
- core waist around 60 mm (unfinished core)
This left a foot print in the mdf board.
All happened about a year ago - now I use ply or skin using ply.
Mdf is made with heat and pressure at around 120 degrees and densities will vary. Some boards have details stamped in to the edge - can't remember what it is about.
Posted: Sun Nov 27, 2011 8:50 am
by rockaukum
These skis were pressed at 60psi at the compressor. I usually press at 40 with no problems but for some reason I went up on the pressure. Again, I think this system works just fine. Not having to make a different mold for each ski is a good time saver not to mention the $ aspect. The shim material I am using is $10 (4x8) at HD. It is a ply used as an underlayment. I do not use a heat blanket (too cheap or don't want to spent the money, yet). I do heat the room with a pellet stove. On those skis the room was at 100* when I went down at night to check on everything. I think one would need to be careful about spacing on the shims to avoid those concerns of indentations. Lastly, I use HDPE as a pressing (cassette) layer.
ra
Posted: Mon Nov 28, 2011 3:57 pm
by Richuk
ra, before you add heat, you may need to alter a few things. The difference in result is probably due to variation is local materials and the thermoplastic nature of the materials being used.
Posted: Mon Dec 05, 2011 6:49 pm
by skisplat
I use the same system with the shims and it works great! For shims, I use 1/8" or 3/16" Masonite cut to various different lengths.
Above the shims (but not shown in the photos) I use 3 layers of 3/4" MDF that are not glued or nailed together. This makes a really thick layer above the shims to avoid the steps pressing through. Having them not nailed or glued allows the MDF layers to sheer and to form more easily to the shape of the shims. I have pressed up to 50 psi and have never had any indentations or "steps" press through to the ski.
**Brainfart alert: When arranging your shims, make sure you create a curve with the shims, and not just a straight line. You have to start with a wide "step", and make each step a little narrower or as you continue in order to create a curve. If your "steps" are the same width, you end up with a straight line. I found this out the hard way. Bonehead.
**Brainfart alert II: Also, make sure you shim the MDF all the way to the ends, (not just under your skis) otherwise the ends of the MDF break off. Found this out the hard way too. Bonehead...again.
Here are the pictures. I usually have 3 layers of MDF above the shims when I press, not just the one layer shown in the photos:
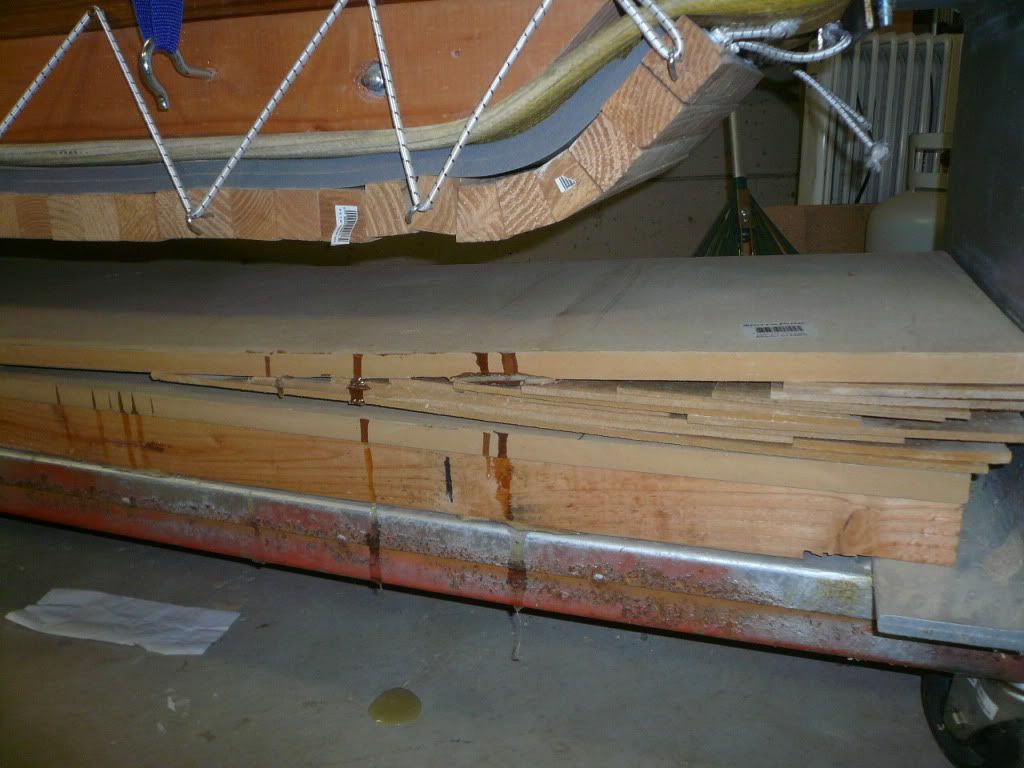
[/img]
It works great, and it really easy and quick to reset for different skis.
Posted: Fri Jan 20, 2012 9:06 am
by bullion mine
I thought about shimming also to change camber but I thought it would not produce even curves due to the pressure (I press at 50 psi / 150 *f. Did anyone shimming have flat spots?