Page 2 of 2
Posted: Mon Sep 05, 2011 10:58 am
by chrismp
it would be great if you could test it with a small sample!
i found a tutorial on how to build such a vacuum chamber and the guy used a small plastic hand pump to pull the vacuum. seemed to work well with silicone resin.
edit: found the link again
http://www.donjarrs-place.com/07-how-to-vacpot
Posted: Tue Sep 06, 2011 6:38 am
by mattman
Not sure if you already know/do this, but when you pour your urethane do you pour high above the part in a very thin stream. This forces many bubbles to escape before entering the part. If you have the time you can also pour into a second cup first and by pouring against the side bubbles are evacuated (like pouring beer).
As far as pulling a vacuum, how about a venturi for your compressor (by hand could be a long process)? Lots of times a polycarbonate plate is placed over a heavy duty mixing tub (with a gasket) to pull a degassing vacuum.
Posted: Tue Sep 06, 2011 7:00 am
by chrismp
thanks a lot for the tips! didn't know the tricks with the pouring...i'll definitely try them!
the venturi is an option i'm considering, but i wouldn't need it that often so i'm not concerned about doing it by hand.
Posted: Tue Sep 06, 2011 7:40 am
by mattman
in that case they have hand vac pumps at auto stores for bleeding brakes (I think, not much of a mechanic). roarockit also has them for pressing longboards. one last tip (we pour lots of urethane parts), pour in one location and let it flow to level...dont move around the board if you can avoid it.
Posted: Fri Dec 30, 2011 4:28 pm
by skidesmond
chrismp wrote:do it like me folks!
i route a channel into the core, pour in some 95A polyurethane resin (adiprene LF950A with e300 hardener...cures well at room temp even if a 16h postcure is recommended! i had the tech guys at chemtura do some testing for me), plane.
sidewalls are the toughest out there and they stick to the core and epoxy like nothing else. plus, you can produce seamless sidewalls/tipspacers. and the stuff is cheaper than buying uhmw sheets. and can be colored with regular epoxy pigments.
Chris,
Question on your pic. I see you created a channel and filled it w/ poly resin. But I don't see how that makes a side wall. Do you flip the board over and plane the board to the specified profile until you see the poly resin? How well does the poly resin plane? Any chipping or tearing?
Any more pics of a finished core?
Thanks
Posted: Sat Dec 31, 2011 12:14 am
by FigmentOriginal
skidesmond wrote:
Any more pics of a finished core?
Or of the finished board?
Posted: Sat Dec 31, 2011 7:47 am
by chrismp
steve, you're spot on! i flip the core over and plane the underside till the urethane shows. usually takes very few passes. then i flip the core over and profile it with a planer jig.
the urethane machines nicely without any tearouts or melting. it doesn't even need flame treating to bond well. the planer gives it a slightly rough surface which is sufficient.
i've built five boards with that type of sidewall and none of them show signs of delamination, even after some heavy park rail abuse.
here's a closeup of the sidewall finish with a router bit (for more pics look at my journal thread):
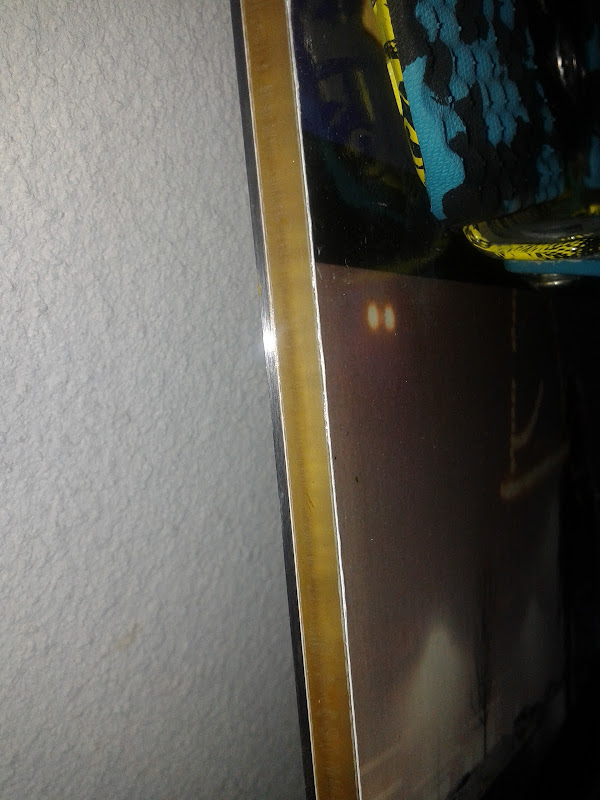
Posted: Sun Jan 01, 2012 11:49 am
by skidesmond
Wow, that looks really nice. I like the wood side walls. I'm still undecided if the masses will find wood side walls too much maintenance, since they are so used to having plastic sidewalls. Too me the only maintenance on wood is a quick wipe down after skiing and annual maintenance. But how many do that?
Good to know there's an alternative to plastic side walls that doesn't look too difficult to do.
Maybe I found another use for my Mirror Coat epoxy.
Posted: Sun Jan 01, 2012 1:26 pm
by chrismp
using urethane has so many advantages if you don't mind the few extra steps.
it's cheaper than uhmpe, easy to use, bonds very well, most durable sidewall material out there, no ripping off sidewalls when planing/routing, seamless sidewall all around the board, adds a bit of dampening...
Posted: Sun Jan 01, 2012 2:06 pm
by vinman
What kind or urethane resin do you use?
Posted: Sun Jan 01, 2012 2:43 pm
by chrismp
it's adiprene lf950a with the e300 hardener.
Posted: Sun Jan 01, 2012 2:51 pm
by vinman
Posted: Fri Jan 06, 2012 9:57 am
by FigmentOriginal
One question for you Chris...when do you cut off the excess of the core? Before or after the planer jig? Before or after you press? How much extra material do you leave on for the flash?
Posted: Fri Jan 06, 2012 11:50 am
by chrismp
@vinman: i can't really tell if this resin would work. it seems a bit hard for me though. i'm using a 95A hardness resin since this is what ride snowboards uses.
their pmc-790 resin seems more suitable, but you better give them a call and ask about the properties of their resin systems in cold conditions. many polyurethanes get brittle at low temps.
@figment: i leave the core completely square the entire process. the excess just gets cut off with the flash. the channel i route into the core is 1/2 inch wide and roughly half of it gets trimmed with the flashing.