Press construction.
Moderators: Head Monkey, kelvin, bigKam, skidesmond, chrismp
-
- Posts: 1354
- Joined: Mon Sep 17, 2007 7:37 pm
Press construction.
Howdy all. Great site here. I love seeing the different equipment you all have built. I have finally decided to build a pneumatic press so I can try and build some snowboards, and maybe some approach skis. My press design incorporates adjustable camber and adjustable / replaceable tip and tail blocks. This design eliminates the ability to use "I"-beams for the base. I am no engineer and unfortunately didn't pay attention in math class. If I am planning on running the press at 70psi and I have a surface area of approximately 1400 square inches how much pressure does the base of the press really need to be able to handle? At this point I was planning on welding a box frame with 2" square 1/4" wall square tube and 1/2" thick steel plate. The camber would be adjustable through solid steel rollers with an offset bolt. There would then be a 3/16" thick steel plate over the top of the solid steel rollers. Essentially all of the pressure from the top form will be transmitted through the mold and the steel plate through the rollers and then the bolts. There will be a total of 24 of these rollers (48 bolts) allowing for a maximum running length of about 180 cm.
24 bolts per side. How big, what grade? Does my press design sound strong enough to handle the pressure? Any ideas / thoughts are appreciated. I will post updates as the project progresses.
24 bolts per side. How big, what grade? Does my press design sound strong enough to handle the pressure? Any ideas / thoughts are appreciated. I will post updates as the project progresses.
-
- Posts: 1354
- Joined: Mon Sep 17, 2007 7:37 pm
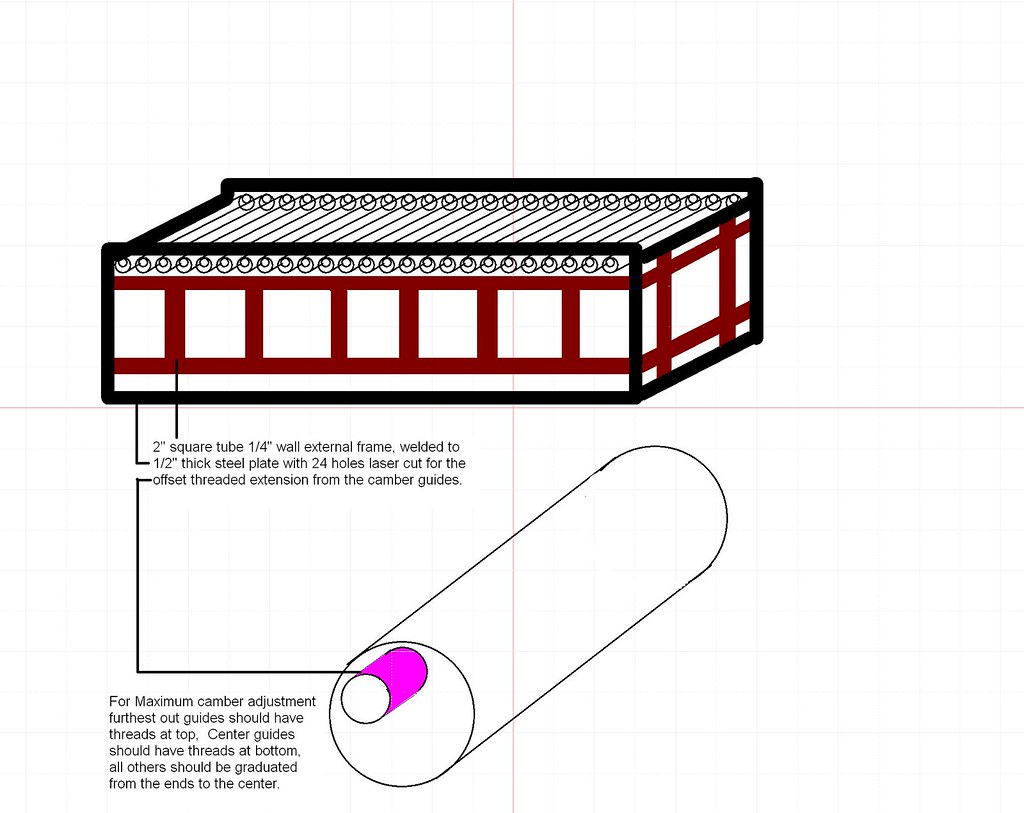
The rollers allow you to adjust for as much camber or rocker as is desired.
I can't imagine that there would be any flex or breakage in the press design with the 1/2" thick steel plate reinforced by the square tube. I think the threads for the roller will need to be at least 3/4" diameter. I will probably have the threads machined out of the solid steel rollers.
I hope that makes a bit more sense.
-
- Posts: 1354
- Joined: Mon Sep 17, 2007 7:37 pm
-
- Posts: 1354
- Joined: Mon Sep 17, 2007 7:37 pm
I left out from my sketch the nuts. One on the inside, one on the outside. By loosening the nuts you can rotate the camber guides. Because the thread is offset, turning the guide changes the height of the guide. There will then be a thin steel plate that sits on the top of the camber guides.
How the forces will work on the thread is my biggest question. My calculations indicate that at 70 PSI, each thread would need to be able to handle 2,500 pounds of pressure. I just don't know if I am right. I multiplied 70 times my surface area in inches then divided by the amount of contact points (threads) and came up with the 2,500lbs of pressure per threaded length.
How the forces will work on the thread is my biggest question. My calculations indicate that at 70 PSI, each thread would need to be able to handle 2,500 pounds of pressure. I just don't know if I am right. I multiplied 70 times my surface area in inches then divided by the amount of contact points (threads) and came up with the 2,500lbs of pressure per threaded length.
Forces are quite high indeed. The concern I have with your setup is that when you will rotate your rolls and get the forces on the sides you will have to find a way to block it in his angle because by just bolting it it will probably start rotating after a while when it loses grip.
For a step-less change of the rotation I don't know what you could do as a solution to this possible problem.
I like the rolls because by putting the steel plate on top of it you get a nice distributed load on a round edge.
Maybe you can put some threaded bars vertically in the structure and in way get the rolls lower or higher by turning the thread. You schould be able to better distribute your load in a vertical rod.
Geoff
For a step-less change of the rotation I don't know what you could do as a solution to this possible problem.
I like the rolls because by putting the steel plate on top of it you get a nice distributed load on a round edge.
Maybe you can put some threaded bars vertically in the structure and in way get the rolls lower or higher by turning the thread. You schould be able to better distribute your load in a vertical rod.
Geoff
-
- Posts: 1354
- Joined: Mon Sep 17, 2007 7:37 pm
Hard to believe how strong grade 8 bolts with a 3/4" diameter are. Supposedly 50,000 lb breaking strength. http://dodgeram.org/tech/specs/bolts/SA ... ength.html
A few words of caution about those bolts specs you linked:
1. I've never seen a Grade 2 bolt (the 1st chart). I wouldn't use an iron bolt either.
2. The bottom chart, with the 3/4 Grade 8 bolts, lists tensile strength. From the looks of your sketch, your bolts will be subjected to shear, not tension.
That looks like a lot of heavy steel rollers, and a lot of machining to get it working. If you have access to the materials and tools to build this, why not just use I-beams?
1. I've never seen a Grade 2 bolt (the 1st chart). I wouldn't use an iron bolt either.
2. The bottom chart, with the 3/4 Grade 8 bolts, lists tensile strength. From the looks of your sketch, your bolts will be subjected to shear, not tension.
That looks like a lot of heavy steel rollers, and a lot of machining to get it working. If you have access to the materials and tools to build this, why not just use I-beams?
As for the whole camber adjustment think I understand your idea in principle but I def think it would shift under load.
I also think that the steel plate/tube frame would bend or break under that much load.
I also feel that if you have the ability and resources to make this complex a system then I would just use I beams and develop a more vertically loaded camber adjustment system.
I also think that the steel plate/tube frame would bend or break under that much load.
I also feel that if you have the ability and resources to make this complex a system then I would just use I beams and develop a more vertically loaded camber adjustment system.
-
- Posts: 1354
- Joined: Mon Sep 17, 2007 7:37 pm
-
- Posts: 1354
- Joined: Mon Sep 17, 2007 7:37 pm
I have finally acquiesced to using I beams for my main construction.
http://www.efunda.com/math/areas/Rolled ... sRltsW.cfm is a list of wide flange beams. I am going to use W10-49 beams. two on the bottom, two on the top. This will give me a 20" width which should work pretty well.
http://www.efunda.com/math/areas/Rolled ... sRltsW.cfm is a list of wide flange beams. I am going to use W10-49 beams. two on the bottom, two on the top. This will give me a 20" width which should work pretty well.
-
- Posts: 1354
- Joined: Mon Sep 17, 2007 7:37 pm
I think I am back on track. After a lot of thought and more perusing of this site and grafs site and I am pretty much sold that I have to have an adjustable camber system or I won't be happy with my press.
G-man used 1/2" grade 8 bolts in his press and figured their shear strength at about 4,000lbs. Assuming this is correct then 48 3/4" bolts would be overkill to handle 75,000lbs of pressure. I don't think I have to worry about their shear strength. I would think that as long as the nut is cranked to a torque setting higher than it's share of the load (1,500lbs) then there shouldn't be any shifting.
I might just have to quit screwing around and build the damned thing.
G-man used 1/2" grade 8 bolts in his press and figured their shear strength at about 4,000lbs. Assuming this is correct then 48 3/4" bolts would be overkill to handle 75,000lbs of pressure. I don't think I have to worry about their shear strength. I would think that as long as the nut is cranked to a torque setting higher than it's share of the load (1,500lbs) then there shouldn't be any shifting.
I might just have to quit screwing around and build the damned thing.