this has been a project of a constantly evolving design, because it boiled down to what planer geometry was and how to retro fit it to meet my needs. one of my critera was to always be able to reverse the "damage" to use the planer as its original use.
i didn't know if the planer head was heavy enough to produce enough downward force to actually cut anything... normally the head is sandwiched between two bolts, but i needed to upper bolt to be removed so the head could travel up freely. the lower bolt would still be adjustable to dictate the lowest position of the planer head.
i removed the upper bolt and tried running a simple plank through it , but unfortunately the weight of the planer head wasn't enough to produce enough downward force and the head lifted up not cutting anything.
so back to the design table: i had to produce more downward force in order to actually plane a sliver of wood. pretty cool considering that the planer head weighs probably 75 pounds. the tolerance and rigidity of the front roller is good, thanks WILTON tools. and i think the forces produced by the wildly fast and powerful blade of the planer head added to the head lifting up.
igneous uses a snow-mobile shock for some of the downward pressure, and i remember their vertical pillars were more sophisticated.
for my extra downward force i used 2 springs that that are held down from above, The springs are beefy and adjustable via a nut/washer on threaded rod. i built a freestanding triangle with threaded rod in the middle for the spring to adjust.
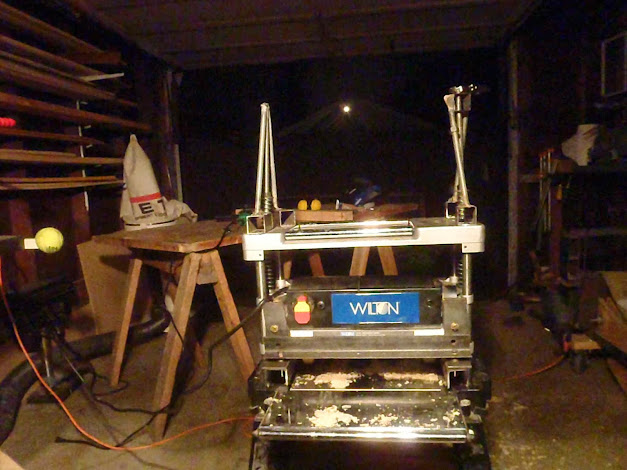

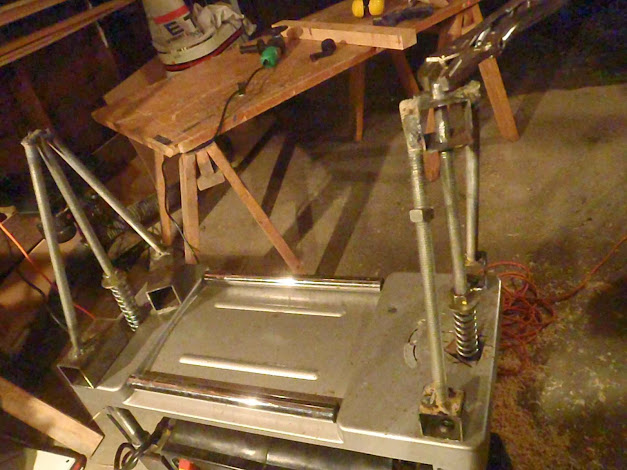
the trial angular shapes are merely bolted to the top of the planer to make for easy removal and turning the planer back into its original shape
notice my turning handle, the planer moves up and down via my vise grips which are an extension from the original. the right one took my thinking then the left one, especially because my design criteria was to make it reversible. some welding in sued, but legal
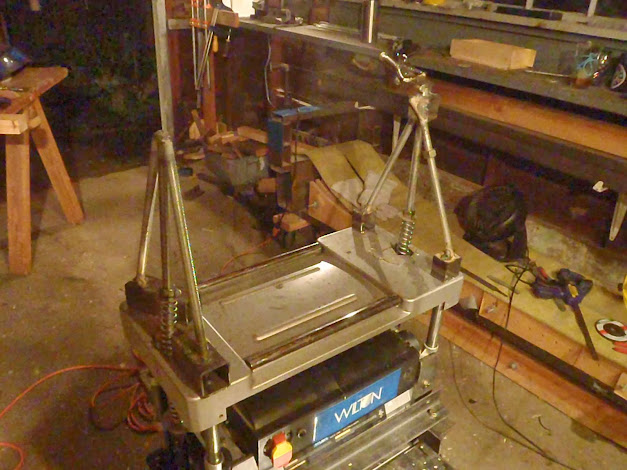
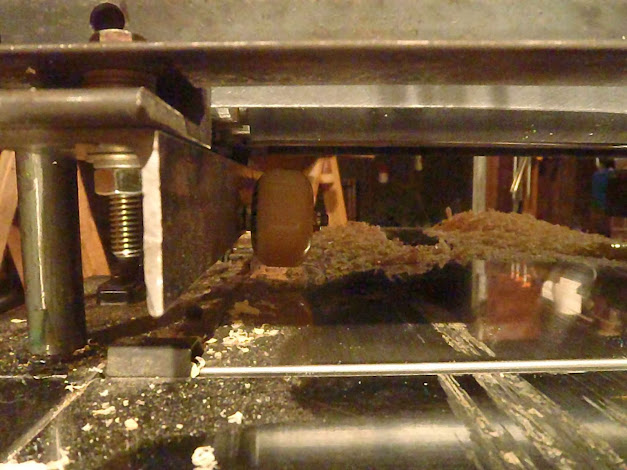

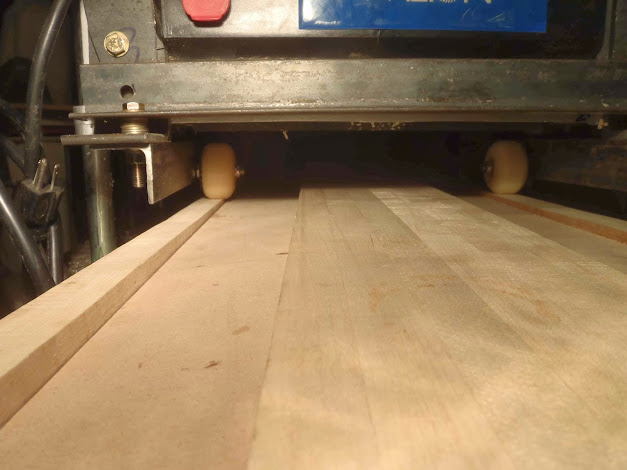
tapered rails
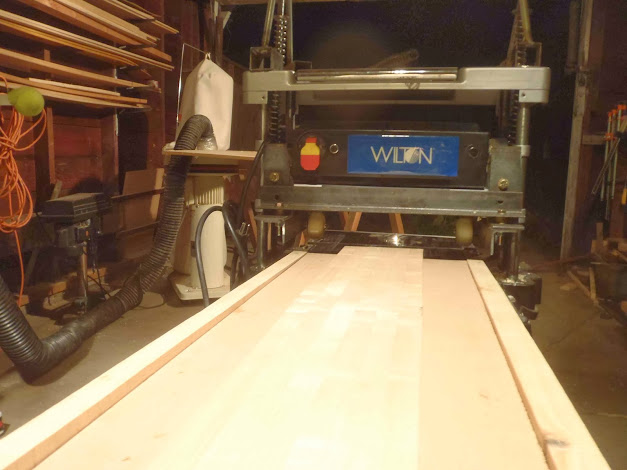
The core sitting in between the rails.
The downward force produced by the springs works well if i am just doing simple planing without the wheels or a jig or anything like that. like as if it were just the top bolt removed and the springs pushing down.
The problem right now is that when the planer head is fully resting on the skateboard wheels and trying to move up past more than 4 or 5 millimeters, there is a lot of of friction and it is causing the core to get stuck inside the planer which causes the feed rollers to "skip" or "burn rubber" on the wood because they aren't strong enough to pull that kind of force.
i am trying to figure out how to reduce friction. For one the skateboard wheels are just bolted on with a nylon locking nut. :c\ which isn't great.
i might be just going back to the router/bridge method