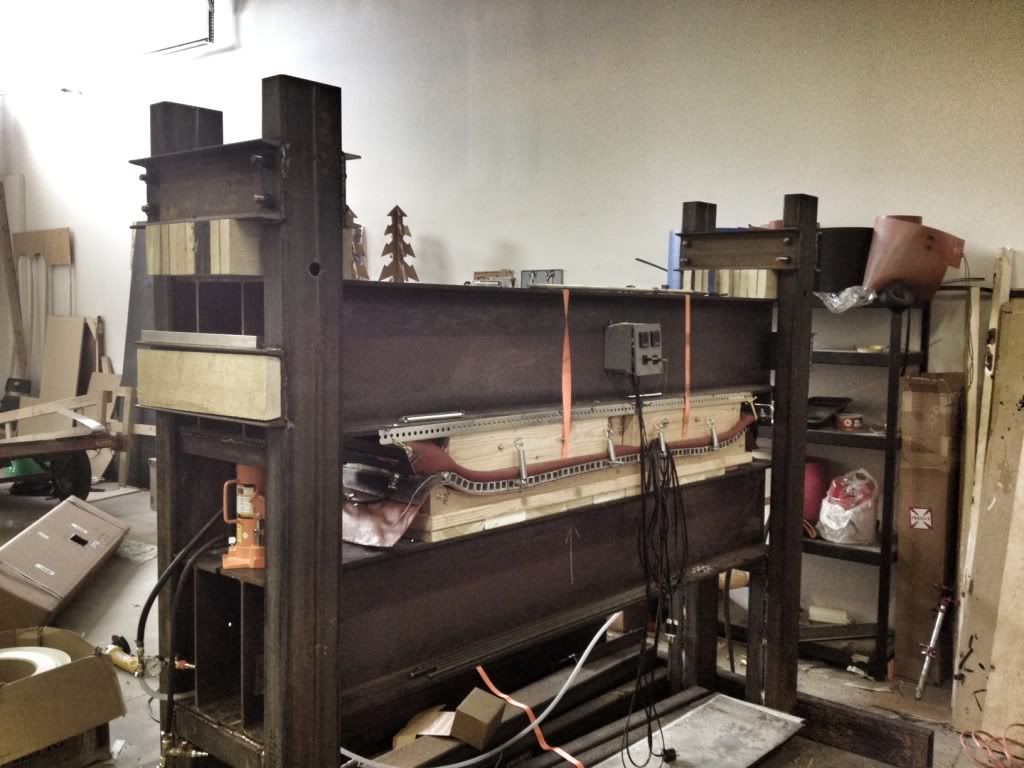
New press design-manual hydraulic
Moderators: Head Monkey, kelvin, bigKam, skidesmond, chrismp
Almost complete. I made a few design revisions. The 1" bar on each side to hold down the press didn't work. The bar deflected quite a bit and I didn't feel comfortable with it. Plan B was to welded some c channel to each side and press with wood spacers under the C-Channel. It didnt hold and the press blew off the welded C-channels! scared the crap out of me and I am lucky it didn't hurt anyone. One thing I have noticed is when I have the bladder fully flattened and inflate the force is dramatically higher than a hose that has 2-3" of slack between the mold. I didn't realize how much area I was losing by not having the hose pressed tight. I used to press at 80psi. Not a chance with this press, I plan on pressing at around 50 psi max. The final design that appears to work and pictured here is the same C-Channels welded and bolted with 5/8" high strength threaded rod. I insert wood blocks in the vacant space. I pressed today upto 50 psi and it didnt budge. 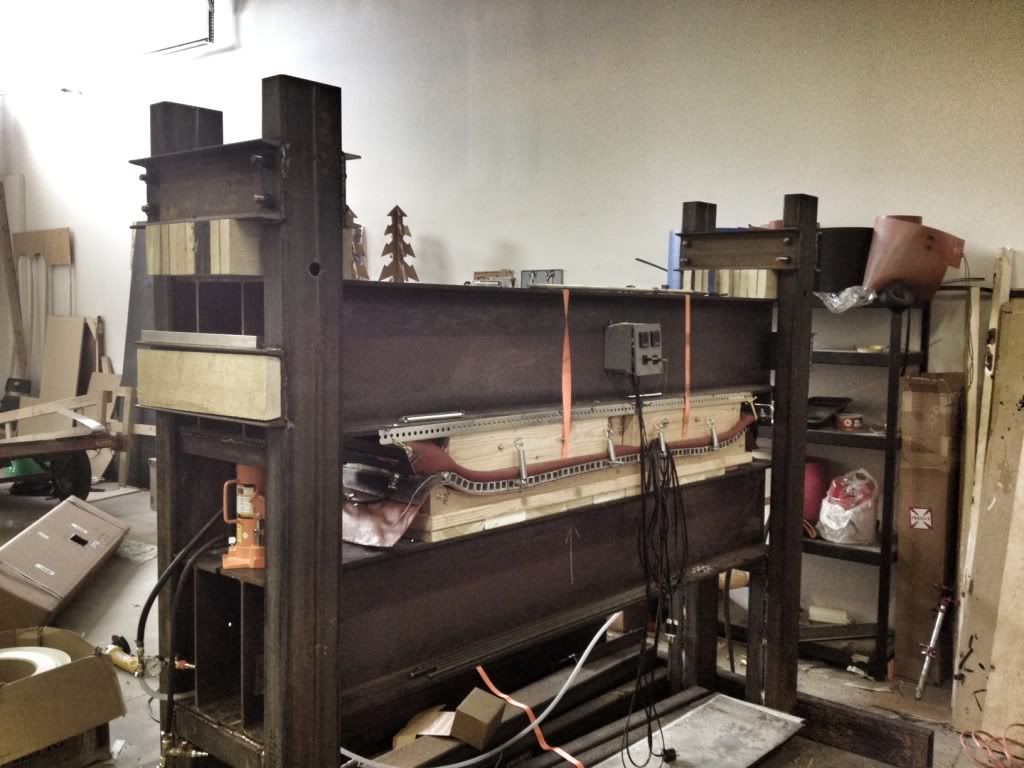
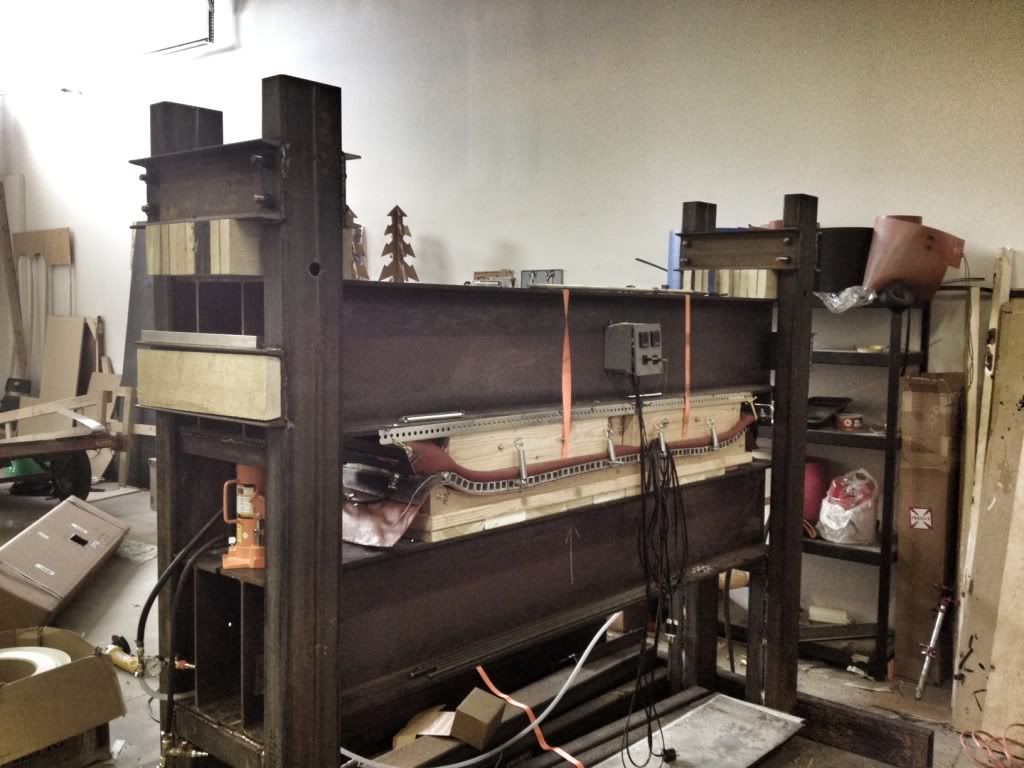
-
- Posts: 66
- Joined: Fri Jun 01, 2012 5:54 pm
Stops.
I have a really similar design for my press that I plan on building. When you were testing the 1" steel rods, how much deflection did they have? My press design was similar but I planned on using two per side with 1-1/4 inch rods, and then welding steel sleeves onto the press frame. Thoughts?
EDIT: Ok so I'd like a few thoughts on this projected 3D drawing of my press, not concerned about opinions on sizes, mainly just the structure and positioning of my end frames. Wondering if the way the C-Channels that support the I-Beams while under pressure should be positions differently or any other opinions.
OP, how did you weld your press? It scares the living hell out of me that some of the channel blew off under pressure, and I'd like to avoid that. Wondering if you think the welds didnt penetrate deep enough or there just wasn't enough support?
Thanks for the help and any opinions, its appreciated!

EDIT: Ok so I'd like a few thoughts on this projected 3D drawing of my press, not concerned about opinions on sizes, mainly just the structure and positioning of my end frames. Wondering if the way the C-Channels that support the I-Beams while under pressure should be positions differently or any other opinions.
OP, how did you weld your press? It scares the living hell out of me that some of the channel blew off under pressure, and I'd like to avoid that. Wondering if you think the welds didnt penetrate deep enough or there just wasn't enough support?
Thanks for the help and any opinions, its appreciated!

It was bowing the 1" rod in the middle by a 1/2"(span of 14") and I stopped. IMO it shouldn't bow/flex at all. You could try 2 rods/side but the problem is if you don't get the holes exactly in the same location when the press starts pushing up it will engage the first bar it hits and will take the majority of the load.When you were testing the 1" steel rods, how much deflection did they have?
Regarding your design: I dont know what to tell you. I am not a welding expert. In fact, this press is the first time I welded and I probably didn't do the best job but I wouldn't rely on just welded connections under the loads we use. Bolts provide so much more strength.
-
- Posts: 1354
- Joined: Mon Sep 17, 2007 7:37 pm
^^^
I agree, my press is 100% welded and there are 0 issues with stability. I have a frame made from 6x6 tube (2 top 2 bottom) stitch welded together and 14 inch H beam sides welded in placed with reinforcement along the side joints of the tube steel and H beam, with center supports front and back. No creaks, no pops, and minimal deflection due to the center posts. I press at 50-60 psi and I feel I could go higher but don't need to with the results I've been getting.
I agree, my press is 100% welded and there are 0 issues with stability. I have a frame made from 6x6 tube (2 top 2 bottom) stitch welded together and 14 inch H beam sides welded in placed with reinforcement along the side joints of the tube steel and H beam, with center supports front and back. No creaks, no pops, and minimal deflection due to the center posts. I press at 50-60 psi and I feel I could go higher but don't need to with the results I've been getting.
Fighting gravity on a daily basis
www.Whiteroomcustomskis.com
www.Whiteroomcustomskis.com
- MontuckyMadman
- Posts: 2395
- Joined: Fri Jun 20, 2008 9:41 pm
-
- Posts: 2337
- Joined: Tue Apr 07, 2009 3:26 pm
- Location: Western Mass, USA
- Contact:
94 - On your press design... You have bottle jacks on the bottom of the press..... I'm assuming they are there to raise and lower the bottom mold.
When you raise the bottom mold and then inflate the hose to 50-60 psi will the bottle jacks be able to hold the bottom mold in place? What's the capacity of the bottle jacks?
When you raise the bottom mold and then inflate the hose to 50-60 psi will the bottle jacks be able to hold the bottom mold in place? What's the capacity of the bottle jacks?
-
- Posts: 712
- Joined: Thu Sep 30, 2010 12:32 pm
- Location: USA
-
- Posts: 66
- Joined: Fri Jun 01, 2012 5:54 pm
Ok to start off Desmond, I'm plan on using two 1-1/4" steel pins that will go underneath the C-channel (the red pieces in the drawing) The bottle jacks are just there to raise and lower the bottom half. I may change the way that I secure the bottom portion of the press after hearing about OP's issues with the pins.
Russian, I'm wanting to use the jacks on the bottom because my press is going to be shorter (8') and I've talked to a few others who have the jacks on the press bed. They ran into some issues where the firehose bladders were obstructed by the jacks. Also the frame will be in my dads shop, and we have quite a bit of room but to maximize storage space, It will be convenient to have the bottom half come out of the press.
Back to the press frame, I think I understand what you mean. Your thinking something along the lines of this on Scott's press?
*PICTURE IS IN THE POST BELOW MINE,THANKS* Instead of having a section of C-Channel below the upper portion of the press, would it be more cost effective to use that material to double up, and then just weld the upper portion of the press to those channels?
Thanks guys! Quick edit here, I noticed that picture is HUGE! Anyway I can downsize it?
Russian, I'm wanting to use the jacks on the bottom because my press is going to be shorter (8') and I've talked to a few others who have the jacks on the press bed. They ran into some issues where the firehose bladders were obstructed by the jacks. Also the frame will be in my dads shop, and we have quite a bit of room but to maximize storage space, It will be convenient to have the bottom half come out of the press.
Back to the press frame, I think I understand what you mean. Your thinking something along the lines of this on Scott's press?
*PICTURE IS IN THE POST BELOW MINE,THANKS* Instead of having a section of C-Channel below the upper portion of the press, would it be more cost effective to use that material to double up, and then just weld the upper portion of the press to those channels?
Thanks guys! Quick edit here, I noticed that picture is HUGE! Anyway I can downsize it?
Last edited by NinetyFour on Sun Jul 01, 2012 12:17 pm, edited 1 time in total.
-
- Posts: 378
- Joined: Wed Nov 04, 2009 10:59 am
- Location: Portland Area, Maine
- Contact:
-
- Posts: 66
- Joined: Fri Jun 01, 2012 5:54 pm
End Frames
Ok so, would like a few opinions on each press design and their endframes. The press on the left will likely be stronger, but will be more restricted with how large my vertical opening can be, and it shortens the size you can side load from by four inches.

Also, instead of pinning the press in place, I think I'm going to have some C-Channel that will sit verticall underneath the bottom part of my press, and it will be held in place with a single bolt so It can't blow out sideways under pressure. Much in the same way that OP has a bunch of wood restricting the upper part of his press.

Also, instead of pinning the press in place, I think I'm going to have some C-Channel that will sit verticall underneath the bottom part of my press, and it will be held in place with a single bolt so It can't blow out sideways under pressure. Much in the same way that OP has a bunch of wood restricting the upper part of his press.
-
- Posts: 712
- Joined: Thu Sep 30, 2010 12:32 pm
- Location: USA
Re: End Frames
94
I'm not sure what you're trying to achieve.
Use of U- channel horizontally in the press not good idea. U-channel probably best profile to use in press which bolted together. If you don't like to use it and going to weld press together other profile combinations can be used. Here example of mine. Vertical part made of 5 inch angle line and top and bottom made of 6" I-beam
BTW did you see is this design?not the press but way to lift upper mold IMO much simpler method to achieve same thing. This is the way I am going. Maybe not the same way because I have no any space between I-beams
http://www.skibuilders.com/phpBB2/viewt ... ght=#30332
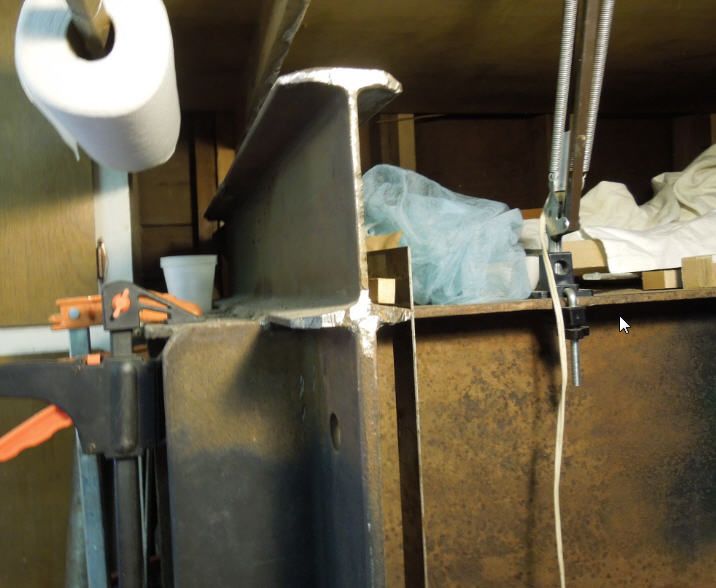
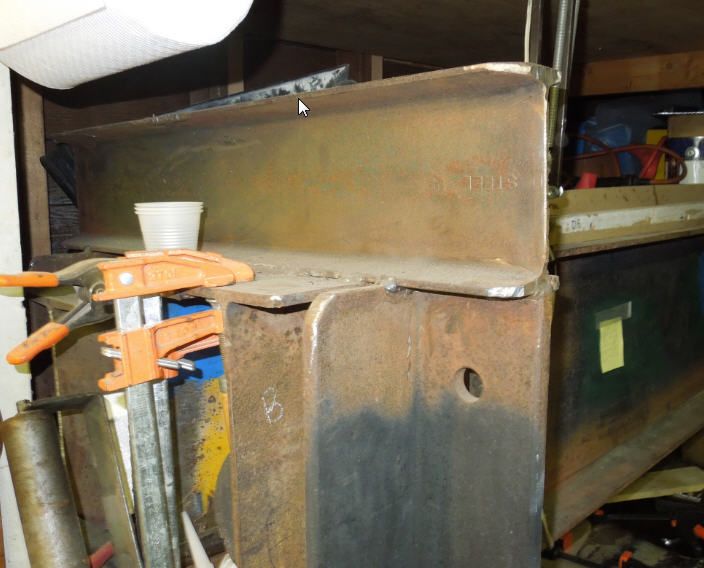
I'm not sure what you're trying to achieve.
Use of U- channel horizontally in the press not good idea. U-channel probably best profile to use in press which bolted together. If you don't like to use it and going to weld press together other profile combinations can be used. Here example of mine. Vertical part made of 5 inch angle line and top and bottom made of 6" I-beam
BTW did you see is this design?not the press but way to lift upper mold IMO much simpler method to achieve same thing. This is the way I am going. Maybe not the same way because I have no any space between I-beams
http://www.skibuilders.com/phpBB2/viewt ... ght=#30332
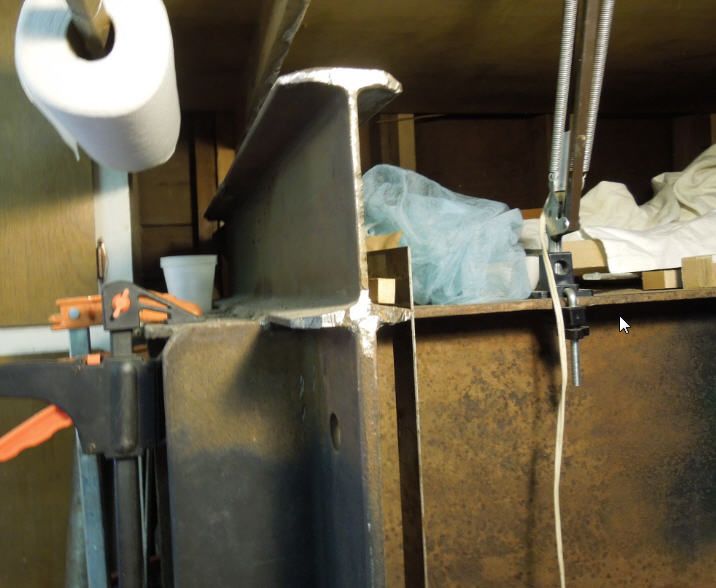
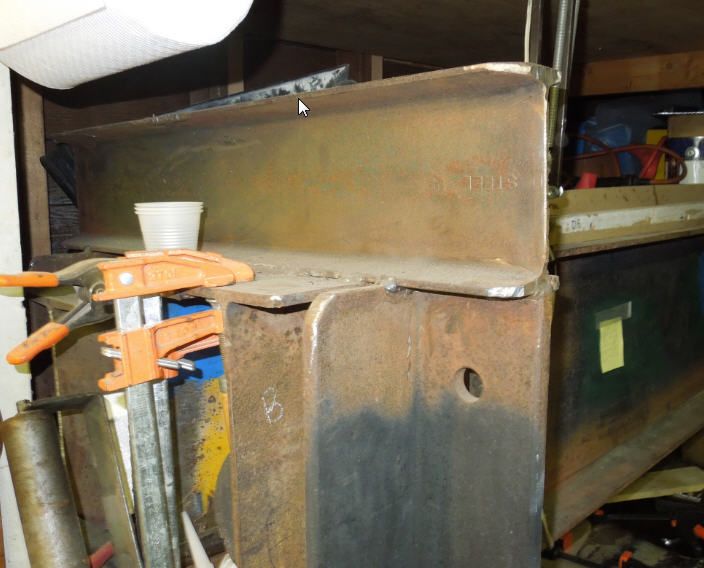
Not many people can do a proper weld that is the problem, especially with mig its far too easy to lay a weld that looks nice but has next to zero penetration. Unless you really know what you are doing with the welder stick to bolts. Even I would use bolts in some circumstances over a weld and I can quite confidently weld.MontuckyMadman wrote:pretty sure a 1" weld is comparable to sheer and load of a grade 8 bolt at the same size. So technically welding will be stronger, if done properly.
FWIW this is a weld I did last week on a boat rudder
