Gonna get in the shop for all the bag people TODAY!
If I am planing a core that is 166cm for a ski to be 186cm
I want to orient my planer jig in what fashion to have them 2.5 in the tip and 13 on center, no flat spot.
its this one:


T = S*Y/X
If S = 1700mm
If x = 830mm
and y = 13mm
then what is T?
26.62mm right? just the height of the shim at the end?-not the overall height of the planer jig.
So, its not planing the same as before. I made the same cores and some others.
I must have done something differently.
Does the overall length of the crib matter and for some reason should mine be longer or shorter?
Should my cores be oriented in another fashion rather than even at the end of the crib?
Why are the cores in this picture hanging off the end of, what appears to be the front on the crib?

Does point A not actually equal 2mm like in the instructions? and the 2mm spot is actually nearer point W and the excess is sniped off?
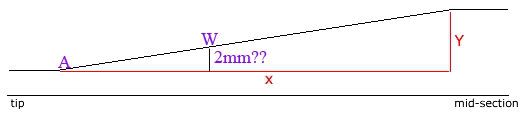
If I want my cores 166 should I start with 186 and cut after planing? I don't think so.
Even with a 21mm shim its still not cutting far enough back towards center.
I know we all did this in 8th grade which is why I am so disappointed in my ability to do this. Just goes to show anyone can build skis.
Please someone spoon feed this info cause I can't get it all of a sudden.
Good thing I have a stack of cores waiting to be ruined.